Published by Angst+Pfister on September 22. 2020
In 2015 at Agritechnica – the world’s largest trade fair for agricultural technology – Krone presented an innovative machine: The first pelletiser to produce pellets in one operation in the field at the moment of harvest that can be delivered straight to retail customers. The “Premos 5000” is hauled by a tractor and gathers straw, which is then compacted into straw pellets by two matrix rollers. The pellets serve both as animal fodder and to heat buildings.
Meeting technical challenges
Krone was seeking a better way to seal the gear unit as dirt found its way too quickly into the internal machine parts, and this overstressed the drive shafts. The metal shaft seal rings in use were not performing to Krone’s high quality standards. The company’s focus is not only on innovative, but also high quality products that are continually being improved – which is exactly what its customers want. This was the background to the managers of Krone contacting Jan-Ole Rienhoff, Product Application Engineer at Angst+Pfister Germany with the question: “Would it work better with rubber?”
Angst+Pfister develops and supplies all types of shaft sealings in a wide variety of sizes for a range of applications, drawing not only from its extensive range of standard products, but also developing custom solutions. “To begin with, we were not one hundred percent certain that we would be able to eliminate this problem,” remembers Jan-Ole Rienhoff. But he wanted to take on the challenge and so discussed openly the potential issues with Krone. The difficulty was primarily the size of the shaft sealings with a shaft diameter of 900 millimetres. The seals need to prevent straw and dirt entering the gear unit, and, conversely, no oil can be allowed to escape the gear unit.
Finding solutions together
The question was what sort of design and suspension preload would increase the seal strength of the two large rings? In addition, they had to be sufficiently robust to get through around a thousand hours before service – one machine is in operation between 200 to 500 hours per season. “Thanks to our know-how, we are also able to tackle technically difficult projects,” says Jan-Ole Rienhoff. The idea was to design a radial shaft seal with metallic reinforcement to maintain its toughness. In order to optimally protect the internal area of the machine, the ring required an axial lip with the addition of grease lubrication to enhance performance. The engineers of Angst+Pfister produced a rough estimate for the design and production of the shaft seal ings. Then it was a matter of looking at the details, making the tools and manufacturing the prototypes.
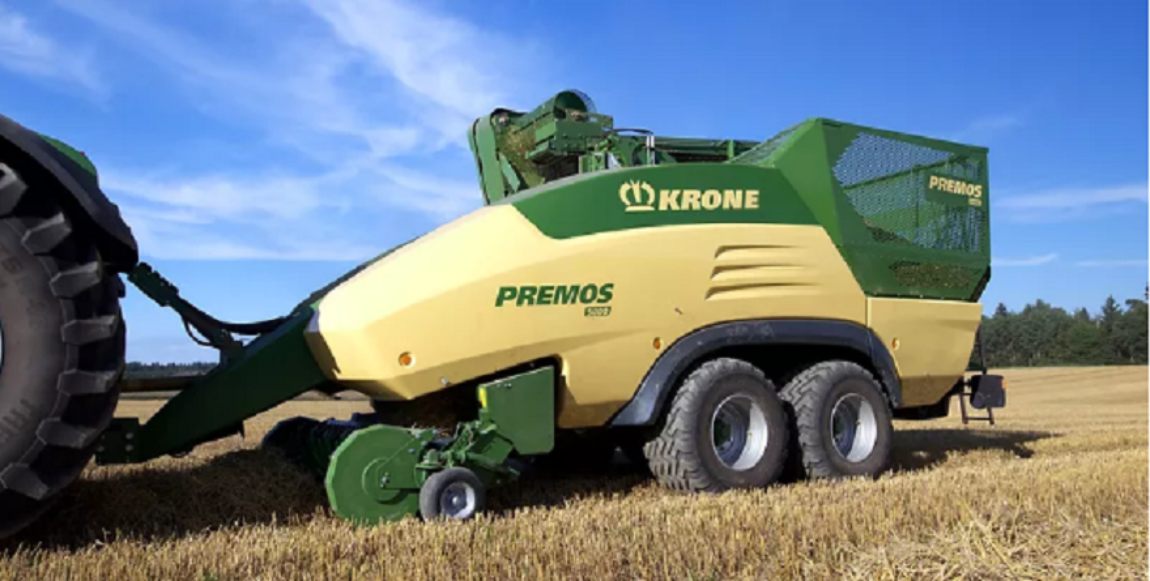
Proactive – from design to installation
Angst+Pfister has an excellent production platform, “So, we were in constant communication with Production,” explains Jan-Ole Rienhoff, who supported the feasibility study to work what, if anything, could be manufactured. Another hard nut to crack was the preload. “If it’s too weak, the seal will not seal correctly – if it’s too strong, it closes too quickly,” explains Jan-Ole Rienhoff.
The first prototype failed immediately because there was straw ingress in the gear unit. Jan-Ole Rienhoff soon found himself in the Krone workshop and together with the customer analysed the contaminated gear unit. The joint analysis and repeat tolerance tests demonstrated that Krone could implement a simple adaptation to the gear unit to increase the preload on the seal lip. The next assembled gear units passed all tests at Krone and are already being deployed by the first farmers. In the meantime, Angst+Pfister has put the shaft sealings into production and supply as a standard product. As an additional service, detailed installation instructions were also provided.
Angst+Pfister came up with the goods to the satisfaction of the customer. “It was important to me that the project was more than working through a list of specifications and that based on our basic knowledge, we discussed the problem together, looked at various ideas and optimisations and jointly developed a solution,” explains Kai Lüpping, who has construction responsibility for the Premos at Krone.
Get connected!
Let’s talk about your challenges and how Angst+Pfister can support you.
Discover Your Path to Innovation
Get to know our expertise in various fields and and partner with us for customized engineering solutions.