Published by Angst+Pfister on February 2021
When young engineers dream of space, Angst+Pfister is happy to make the dream a reality – with lots of down-to-earth technical experience for their special requirements. Students of the Swiss ARIS Space and Rocket Project looked to Angst+Pfister for seals in their bid to win an international rocket competition.
An ambitious team of students from the ETHZ Swiss Federal Institute of Technology in Zurich is reaching for the stars – following in the footsteps of Switzerland’s internationally-renowned education establishments, which have produced no less than 21 Nobel Prize winners. The students plan to launch a hybrid rocket in a far off place where the air is very thin.
De toekomst afdichten
Toekomstbestendige afdichtingen voor drinkwater
In het steeds veranderende landschap van regelgeving staat de drinkwaterindustrie voor nieuwe uitdagingen met de op handen zijnde "beoordelingsgrondslag voor kunststoffen en andere organische materialen die in contact komen met drinkwater" (KTW-BWGL) die vanaf 1 maart 2025 wettelijk bindend wordt in Duitsland. Vooruitlopend op deze veranderingen heeft Angst+Pfister een innovatief elastomeer geïntroduceerd, HITEC® DW EPDM, dat is ontworpen om te voldoen aan de strenge normen van morgen en deze zelfs te overtreffen, terwijl het superieure mechanische eigenschappen biedt.
De toekomst afdichten
Toekomstbestendige afdichtingen voor drinkwater
In het steeds veranderende landschap van regelgeving staat de drinkwaterindustrie voor nieuwe uitdagingen met de op handen zijnde "beoordelingsgrondslag voor kunststoffen en andere organische materialen die in contact komen met drinkwater" (KTW-BWGL) die vanaf 1 maart 2025 wettelijk bindend wordt in Duitsland. Vooruitlopend op deze veranderingen heeft Angst+Pfister een innovatief elastomeer geïntroduceerd, HITEC® DW EPDM, dat is ontworpen om te voldoen aan de strenge normen van morgen en deze zelfs te overtreffen, terwijl het superieure mechanische eigenschappen biedt.
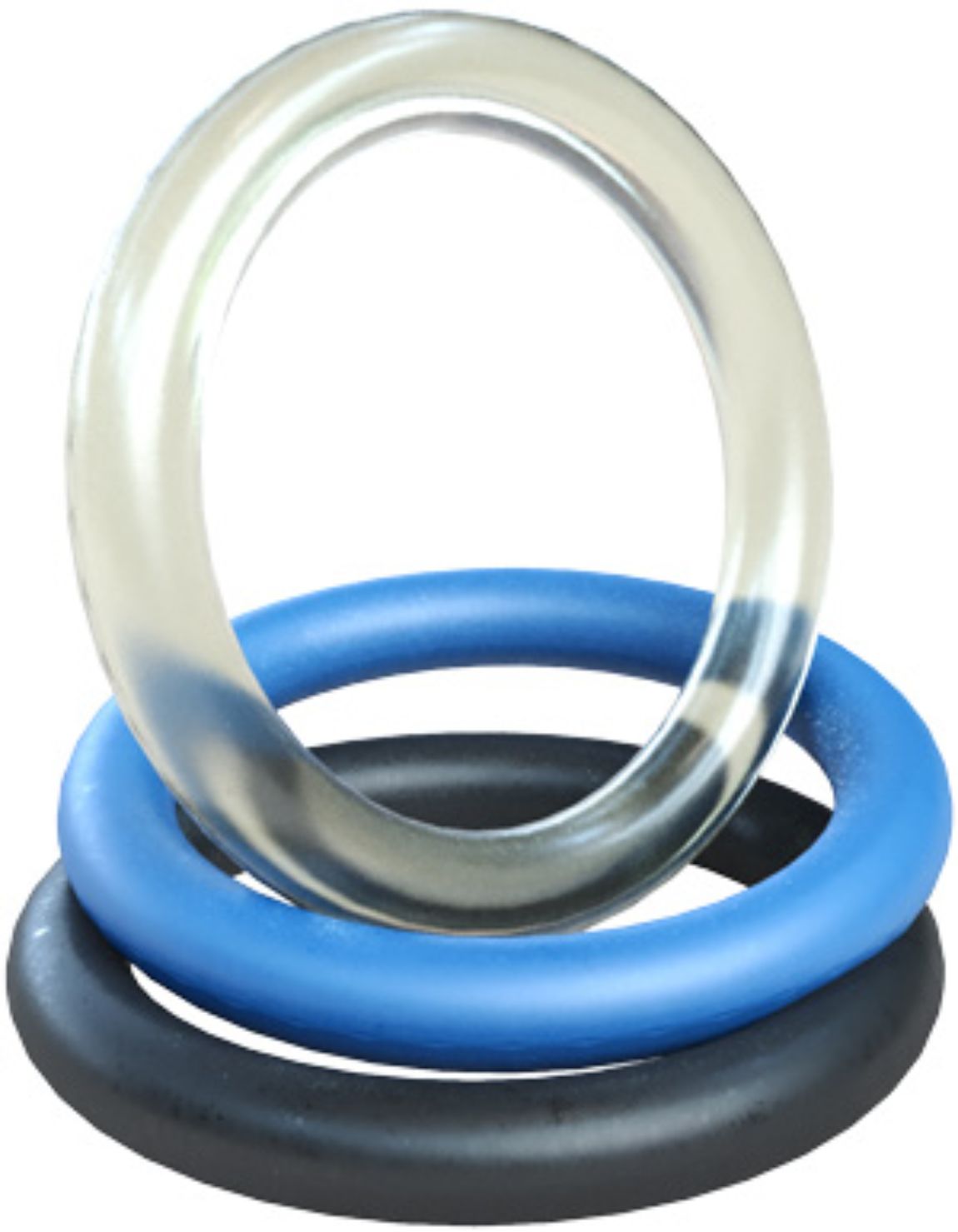
Materials for top performance
The students also needed special materials that are able to withstand extreme stress. Yves Riedo reached deep into the vaults: “One of the materials we used was Kalrez® with a selling price of several thousand euros per kilogramme.” The material allowed the students to carry out the maximum number of tests – without having to replace the seals and dismantle the engine every time. “If you want to win, you have to be better than the competition,” says Yves Riedo with a twinkle in his eye. The engine required a complete sealing system of 17 O-rings in six different dimensions, and a combination of five different materials. There had to be seals between the injector and combustion chamber, the combustion chamber and outlet nozzle, for the cooling system within the nozzle with the connections to the casing and the plenum chamber, as well as for diverse sensors within the injector (see illustration). In addition to the Kalrez® (FFKM) already mentioned, an ethylene propylene diene monomer elastomer (EPDM), a fluoroelastomer (FKM) and a fluoroelastomer (FKM) with a seamless FEP lining (FEP-O-SEAL®) were used.
The engine will be filled with an explosive oxidising agent that is warmed to reach a pressure of around seventy bar. In operation minus temperatures are encountered briefly in the injector and also temperatures up to +2800 degrees in the combustion chamber. Consequently, the sealing system will be confronted with conditions of extreme chemical and thermal stress and needs to function reliably several times. “We use nitrous oxide as the oxidising agent combusted with sorbitol. It also contains paraffin and aluminium,” says the ETHZ student. “The special material that we selected to use gives us a clean seal on the copper outlet nozzles no matter how high the temperatures or size of expansion gap. The seals on the injector, meanwhile, fulfil the requirements of nitrous oxide fully.” With New Mexico clearly in sight: It’s not going to be a matter of the materials.
Kalrez® is a DuPont™ brand. DuPont™, the DuPont Oval Logo, and all trademarks and service marks denoted with ™ or ® are owned by affiliates of DuPont de Nemours, Inc.
Engine cross-section
On the left is the injector plate for the liquid oxidising agent that on injection is atomised and vapourised. The injector has to remain sealed for both physical states. The oxidising agent then reacts with the gradually vapourising fuel (grain) in the combustion chamber. Pressure is generated by combustion of the gas mixture, which is transformed into kinetic energy by means of the copper Laval nozzles. And in accordance with the rocket principle produces the thrust of the engine.
The engine will be filled with an explosive oxidising agent that is warmed to reach a pressure of around seventy bar. In operation minus temperatures are encountered briefly in the injector and also temperatures up to +2800 degrees in the combustion chamber. Consequently, the sealing system will be confronted with conditions of extreme chemical and thermal stress and needs to function reliably several times. “We use nitrous oxide as the oxidising agent combusted with sorbitol. It also contains paraffin and aluminium,” says the ETHZ student. “The special material that we selected to use gives us a clean seal on the copper outlet nozzles no matter how high the temperatures or size of expansion gap. The seals on the injector, meanwhile, fulfil the requirements of nitrous oxide fully.” With New Mexico clearly in sight: It’s not going to be a matter of the materials...
Conclusion
The journey to space is fraught with complexities, from the precise engineering of rocket engines to the unforgiving environment of the cosmos. Yet, through collaboration and shared passion, the team has navigated these challenges with determination and ingenuity. The ARIS project represents not only a quest for scientific advancement but also an opportunity to inspire future generations and redefine the boundaries of what is possible.
As the team sets its sights on the Spaceport America Cup in New Mexico and beyond, the partnership between Angst+Pfister and the ETHZ students serves as a beacon of innovation and cooperation in the pursuit of exploration. Together, they are proving that with dedication, expertise, and a shared vision, even the stars are within reach.
Wij zorgen dat het werkt
Neem gewoon contact met ons op en we nemen snel contact met u op!
Ontdek uw weg naar innovatie
Maak kennis met onze expertise op verschillende gebieden en ga met ons in zee voor engineeringoplossingen op maat.