Um die beste Lösung für unsere Kunden zu entwerfen und zu entwickeln, nutzt Angst+Pfister die neuesten CAD-Softwaretools für Lebensdauersimulation und Leistungsoptimierung. Dieser Ansatz stellt sicher, dass jedes Produkt bis ins kleinste Detail sorgfältig entworfen wird, bevor es in Produktion geht.
Durch die Integration der Finite-Elemente-Methode (FEM) simulieren wir die Leistung und optimieren die Konstruktionen im Hinblick auf Langlebigkeit und Effizienz. Dieser Ansatz ermöglicht eine präzise Materialauswahl und Konstruktionsvalidierung, wodurch das Risiko von Ausfällen in kritischen Anwendungen erheblich reduziert und höchste Qualität und Zuverlässigkeit gewährleistet werden.
Schlüsselkompetenzen auf einen Blick
- Designvalidierung: Durch die nahtlose Integration von CAD, FEA und Mold-Flow-Analyse wird sichergestellt, dass die Entwürfe vor Produktionsbeginn auf Langlebigkeit, Effizienz und Herstellbarkeit optimiert werden.
- Verbesserte Zuverlässigkeit und Langlebigkeit: Durch präzise Materialauswahl und Leistungssimulation wird das Ausfallrisiko bei kritischen Anwendungen erheblich reduziert, sodass Lösungen mit überlegener Zuverlässigkeit und verlängerter Lebensdauer entstehen.
- Beschleunigter Entwicklungsprozess: Fortschrittliche Simulationstechnologien minimieren die Prototypen- und Testzyklen und ermöglichen eine schnellere Markteinführung, ohne Kompromisse bei Qualität oder Präzision einzugehen.
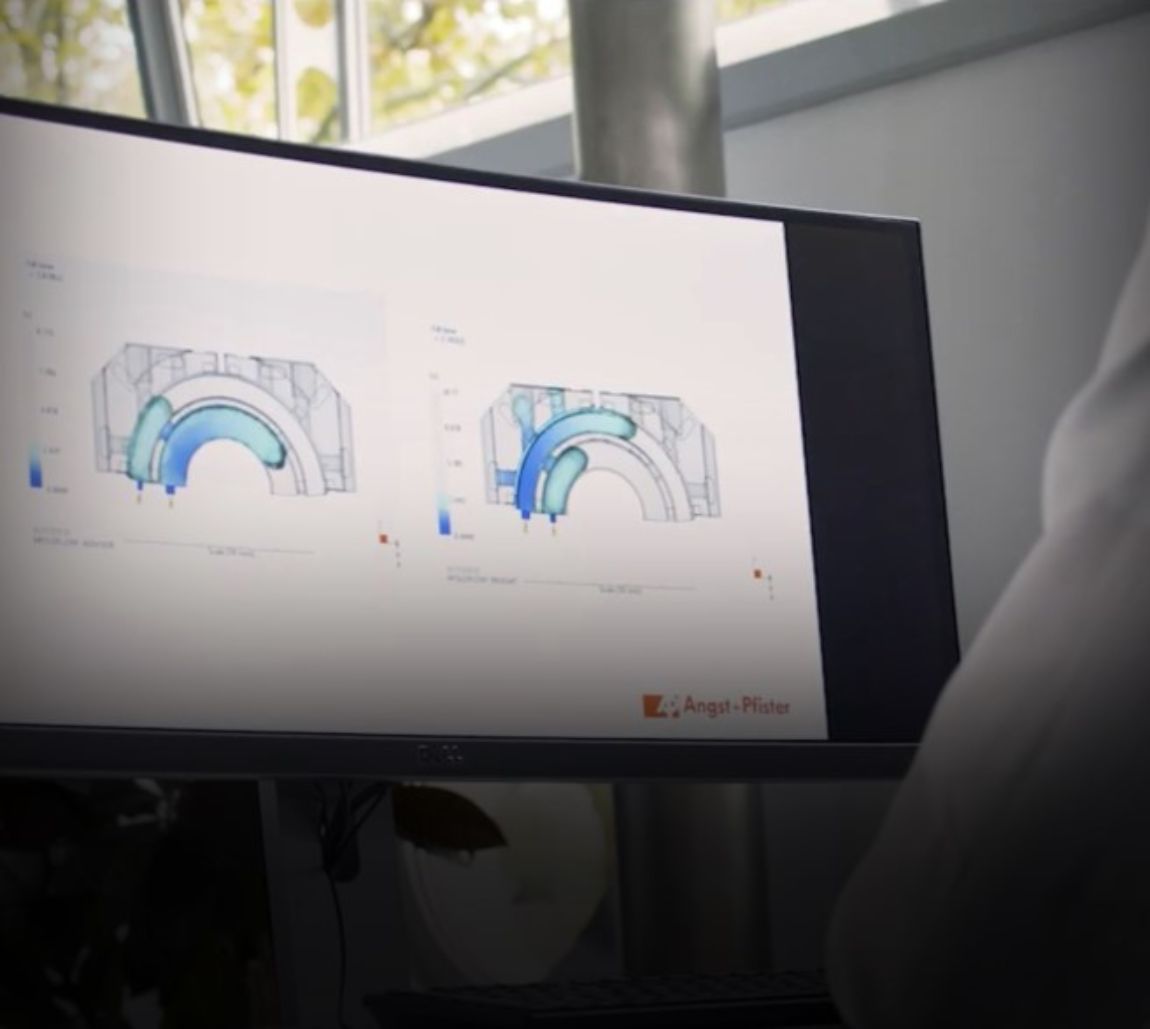
Präzision bei jedem Schritt – der Prozess der Lösungskonzeption und -entwicklung
Schritt 1 – Erstellen von 2D-Zeichnungen und 3D-Baugruppen
Wir beginnen mit computergestütztem Design (CAD) und nutzen fortschrittliche Software, um hochpräzise 2D-Zeichnungen und 3D-Baugruppen zu erstellen. Dieser grundlegende Schritt ermöglicht es uns, jedes Detail des Entwurfs zu verfeinern und die Voraussetzungen für nachfolgende Analysen zu schaffen, die die Funktionalität und Herstellbarkeit optimieren.
Schritt 2 – Einsatz der Finite-Elemente-Methode
Als Nächstes setzen wir die Finite-Elemente-Methode (FEM) ein, um kritische physikalische Verhaltensweisen während der Entwurfsphase zu simulieren. Durch die Analyse von Spannungs-/Dehnungsreaktionen, Wärmeausdehnung und Schrumpfung gewinnen wir wertvolle Erkenntnisse, die den Bedarf an umfangreichen Prototypen und Tests minimieren. Dadurch können wir besser optimierte Komponenten in kürzerer Zeit entwickeln.
Schritt 3 – Sicherstellung eines optimalen Materialflusses und Funktionalität
Um den Herstellungsprozess für Gummikomponenten zu perfektionieren, führen wir mithilfe einer virtuellen Spritzgusssimulationssoftware Simulationen des Spritzgusszyklus durch. Detaillierte Farbkarten zeigen wesentliche Daten zu Temperatur, Wärmefluss, Füllmustern und Spritzdruck innerhalb der Form. Diese Erkenntnisse helfen uns, einen optimalen Materialfluss, Funktionalität und einheitliche Qualität in allen Hohlräumen sicherzustellen.
Lassen Sie uns über Ihr Projekt sprechen!
Fordern Sie ein kostenloses Beratungsgespräch an und finden Sie eine perfekte, auf Sie zugeschnittene Lösung.
Auf der Basis unseres Sortiments entwickeln wir eine individuelle Lösung für Ihre Anwendung - oder wir entwickeln sogar von Grund auf ein Hochleistungsteil für Ihr Produkt, um Qualität und Sicherheit zu gewährleisten. Für kompetente Beratung und massgeschneiderte Lösungen, die auf Ihre spezifischen Bedürfnisse zugeschnitten sind, sind die Serviceangebote von Angst+Pfister.
Termin vereinbaren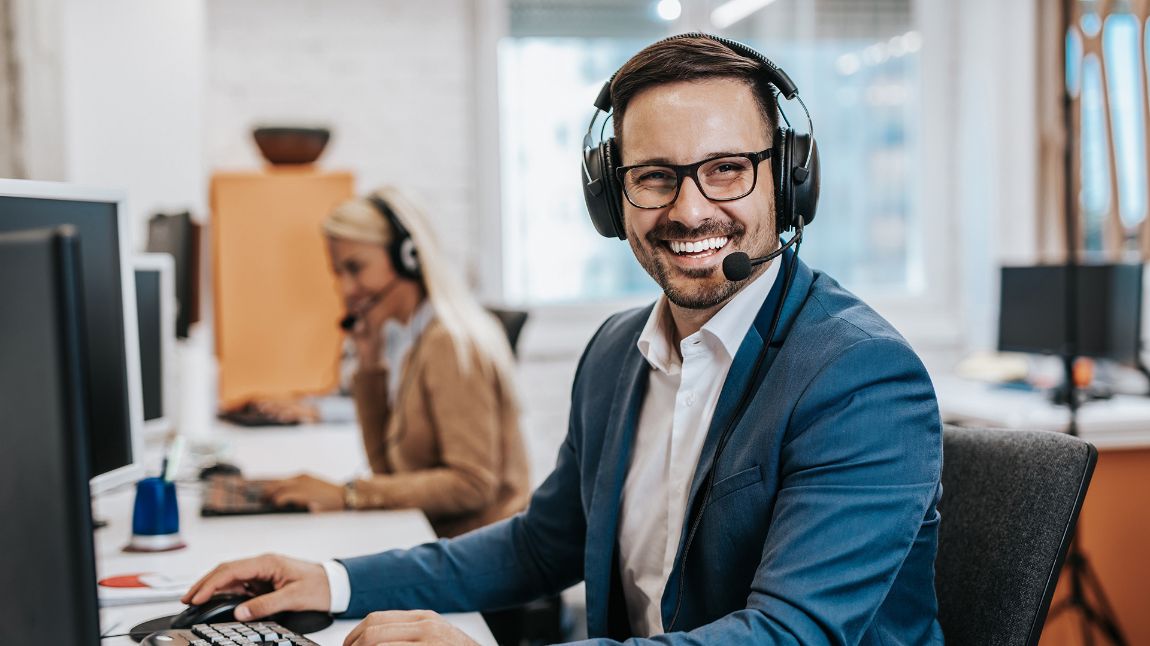
Steigern Sie Ihre Leistung mit unseren Lösungen
Wir sorgen dafür, dass es funktioniert!
Nehmen Sie einfach Kontakt mit uns auf und wir werden uns so schnell wie möglich bei Ihnen melden!
Bleiben Sie auf dem Laufenden!
Melden Sie sich noch heute für unseren Newsletter an und erhalten Sie unsere neuesten Informationen über Produkte und Branchentrends!