In the demanding world of oil and gas, equipment must endure some of the harshest conditions on the planet. Applications in this industry expose machines and components to extreme pressures, aggressive chemicals—including complex mixtures of hydrocarbons, H₂S, CO₂, methane, and amine-based corrosion inhibitors—as well as superheated steam, high pressures, and temperatures ranging from well below 0°C to over 200°C. Safety and reliability aren’t just requirements; they are the foundation of safe and efficient operations, from exploration to refining.
Main Challenges in the Oil and Gas Industry
Corrosion and Abrasion Resistance
Corrosion and abrasion in oil and gas are major challenges due to exposure to corrosive chemicals, high pressures, abrasive particles, and extreme temperatures. These harsh conditions accelerate wear, leading to issues like pitting, stress corrosion cracking, and erosion in critical components such as pumps, valves, and seals, ultimately compromising equipment longevity, operational efficiency, and safety.

High Pressure and High Temperature
High pressure and high temperature (HPHT) conditions in oil and gas operations present severe challenges, stressing materials and equipment to their limits. Extreme pressures can induce structural deformation and fatigue, while high temperatures accelerate chemical reactions, corrosion rates, and material degradation. Combined, HPHT conditions push components toward failure, risking leaks, efficiency loss, and costly downtime in critical applications.
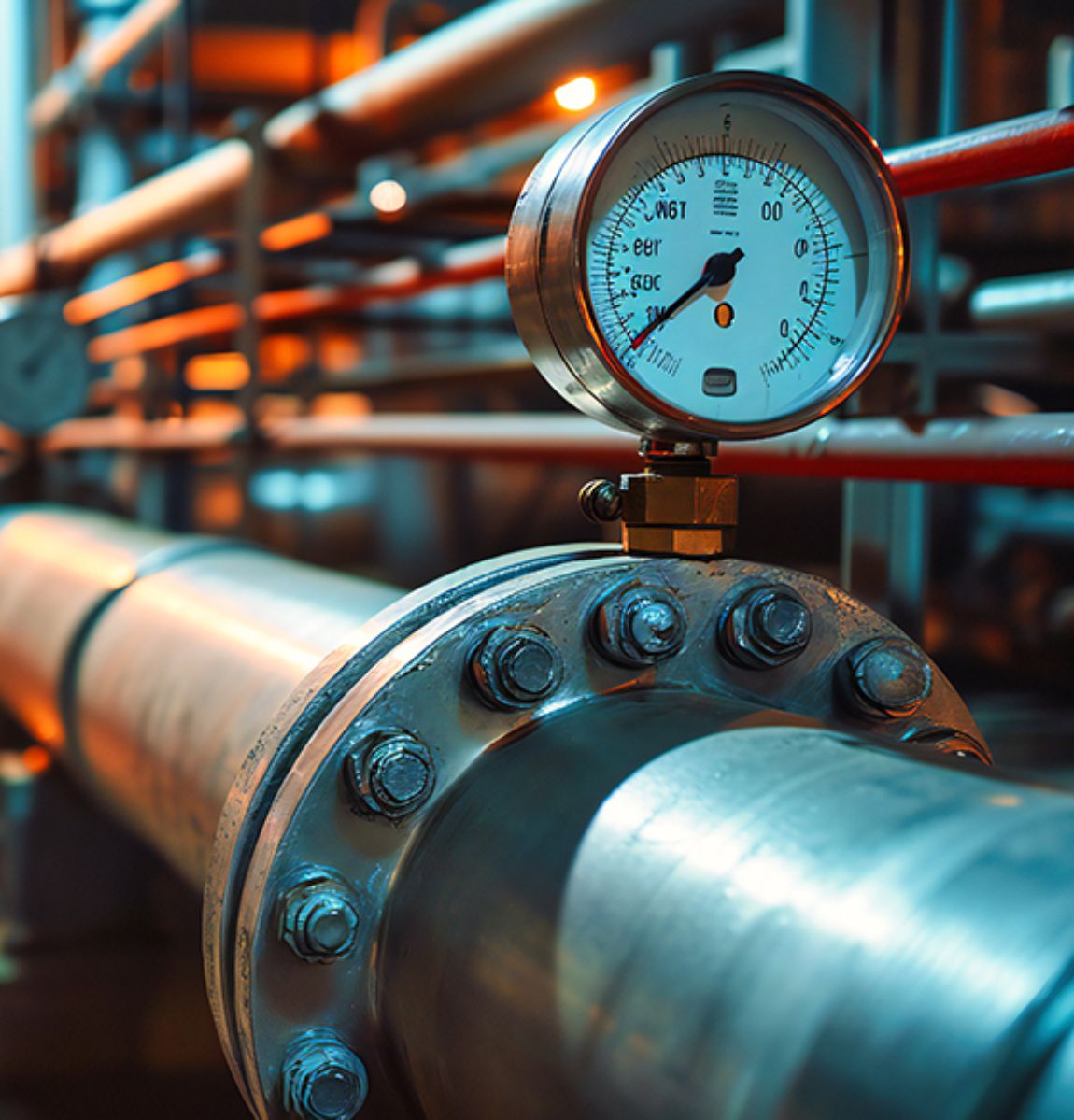
Rapid Gas Decompression (RGD)
A critical challenge in oil and gas, occurring when high-pressure gas absorbed into materials—especially elastomers—suddenly expands as external pressure drops. This rapid expansion can cause blistering, cracking, or even explosive rupture in seals and components. RGD compromises the structural integrity of equipment, leading to potential leaks, reduced operational safety, and increased maintenance demands.
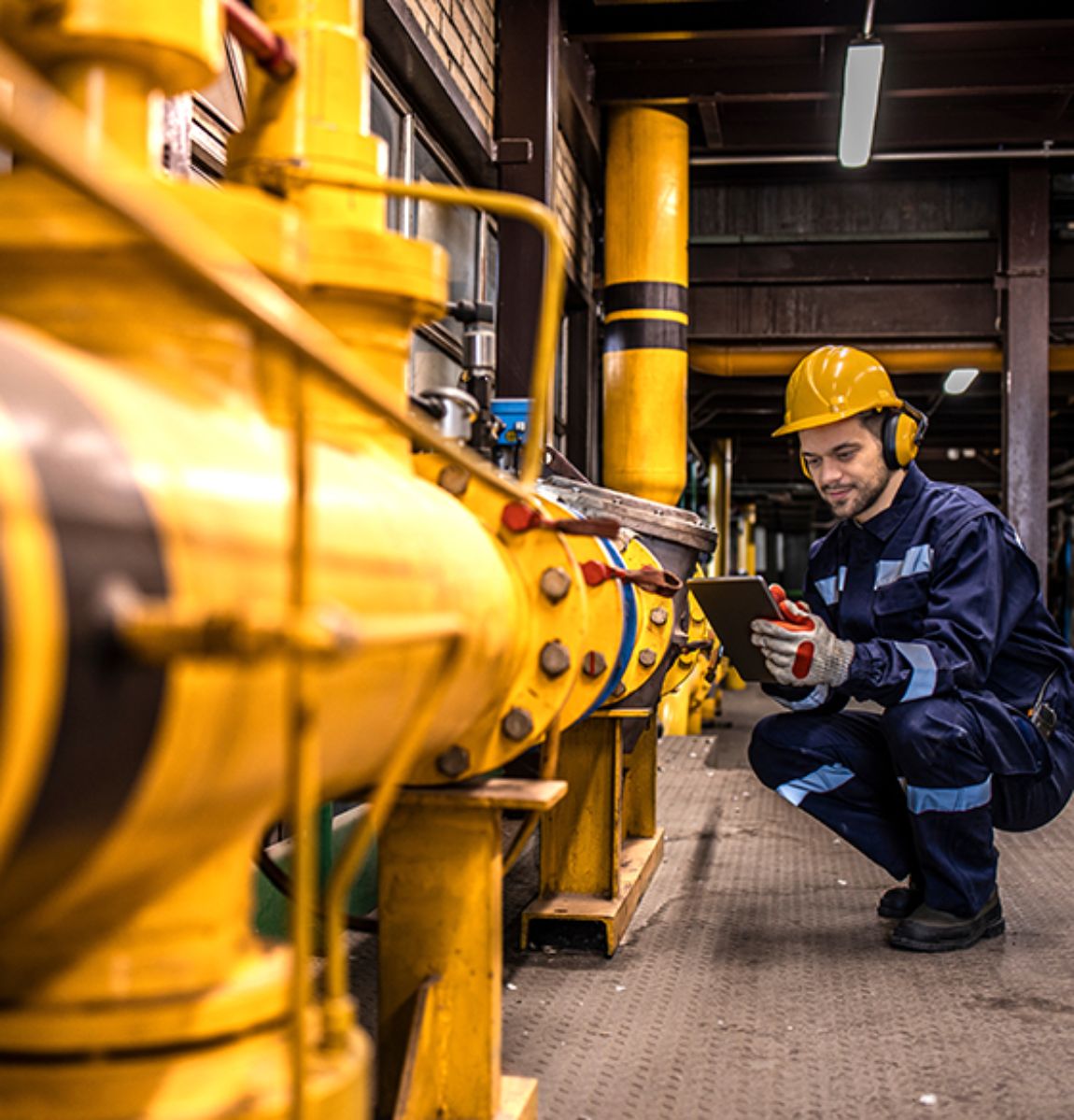
Dynamic Movements and Mechanical Stress
Dynamic movements and mechanical stress in oil and gas operations place intense demands on components, as constant vibrations, shifting loads, and rotational forces generate wear, fatigue, and deformation. High-impact forces, repetitive motion, and sudden load changes can cause material fatigue, micro-cracking, and surface erosion. Over time, these stresses compromise component integrity, increasing the risk of failure, leaks, and costly downtime.
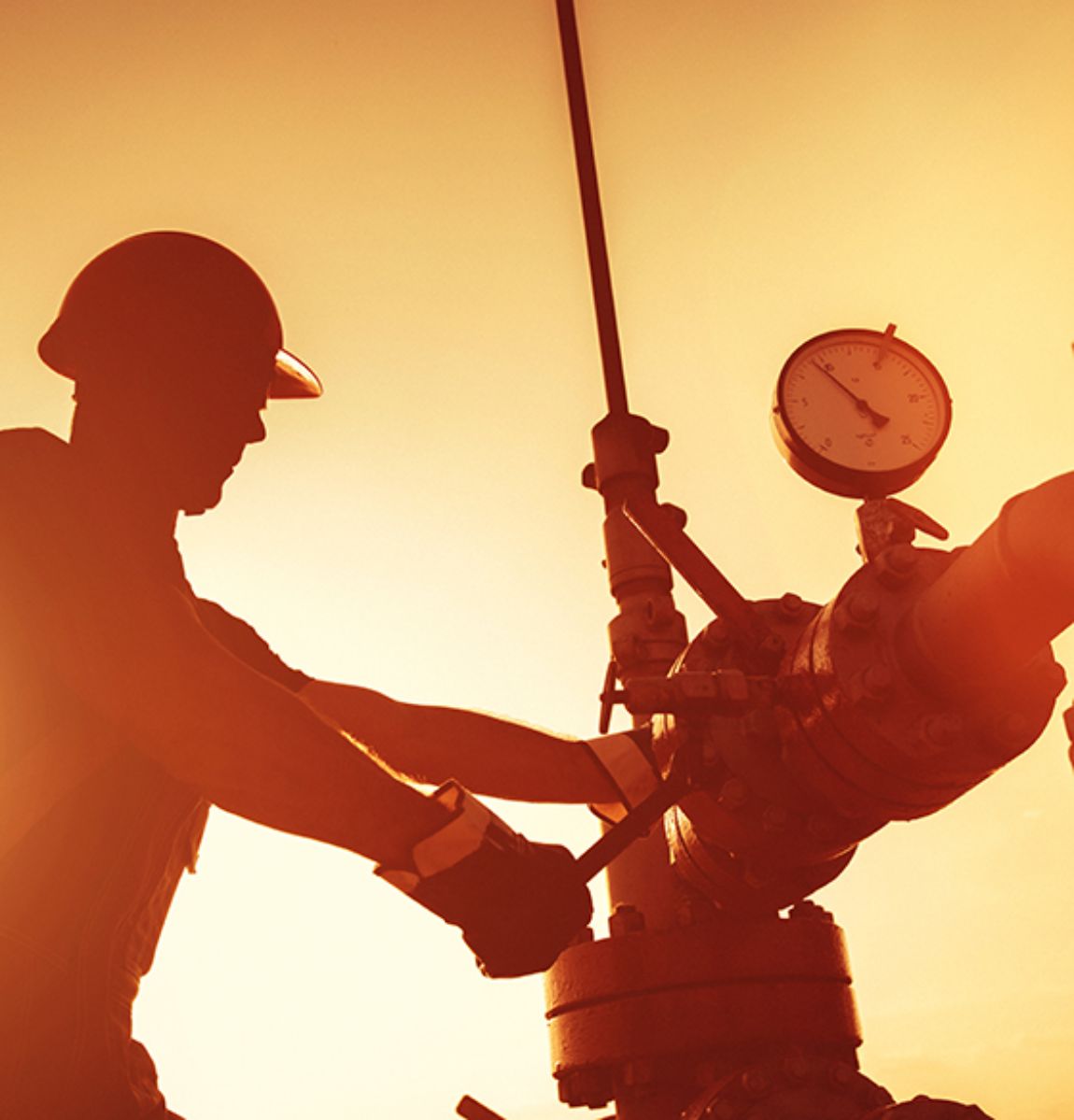
The Right Choice from the Start - Angst+Pfister's Solutions for the Oil and Gas Industry
How Angst+Pfister’s Solutions Are Being Applied:
- Sealing Solutions for Harsh Environments: Our seals provide reliable performance in high-pressure, high-temperature environments, with resistance to extrusion and aggressive media.
- Seals for Gas Leak Prevention: We offer sealing materials designed to minimize environmental impact, ensuring that gas leaks are reduced and regulatory compliance is met.
- Hydrogen and CO2 Applications: New materials developed specifically for H2 and CO2 environments are now available, ensuring safe and effective operation in these emerging energy sectors.
- Maintenance Reduction: Our seals help extend equipment lifespan by reducing the need for frequent repairs and replacements, leading to significant cost savings over time
Customer Benefits:
- Regulatory Compliance: Our sealing solutions are certified by major energy players, ensuring compliance with industry regulations and helping to minimize environmental contamination and gas leaks.
- Enhanced Safety: Designed to withstand extreme conditions, our seals offer high pressure, high-temperature, and extrusion resistance, ensuring safety in hazardous environments.
- Cost Savings: By reducing maintenance, repair expenses, and the need for frequent replacement parts, our solutions help extend the lifespan of equipment and deliver long-term cost savings.
- Advanced Materials for Emerging Markets: We offer newly developed and approved materials specifically designed for hydrogen (H2) and carbon dioxide (CO2) environments.
- Long-Term Reliability: Our seals are engineered for durability and longevity, enhancing system performance in challenging conditions and minimizing operational downtime.
For more detailed information on our specialized solutions for the Oil and Gas industry, please visit the websites of our group entities, MCM and O.L. Seals, to explore our full range of products and services.
Proven Success in Motion - Our Customer Stories
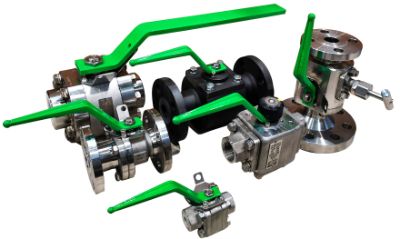
We Solve the Complexity of the Oil and Gas Regulation Jungle
Angst+Pfister provides a wide range of global certifications for the oil and gas industry to ensure safety, reliability, and compliance in challenging environments. Key certifications include NORSOK M-710 for material resistance, NORSOK M-630 for mechanical integrity, and ISO 5208 for valve testing. We also meet critical API standards, such as API 622, 6A, and 6D, as well as ISO 15848-1 for low emissions and ISO 23936-2 for non-metallic materials. With additional certifications like NACE for corrosion resistance and BS 6364 for cryogenic valves, our components meet the highest standards, supporting reliable, compliant operations worldwide.
Boost Your Performance With Our Solutions
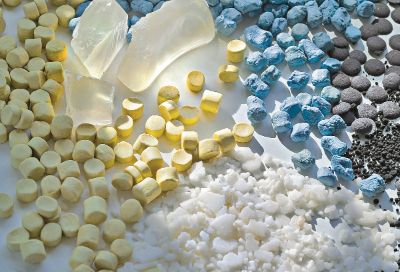.jpg)
Innovative elastomers determine the future of sealing technology.
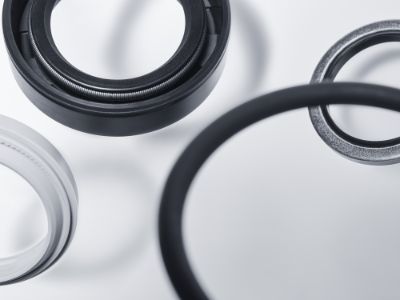
A comprehensive o-ring- and molded part assortment
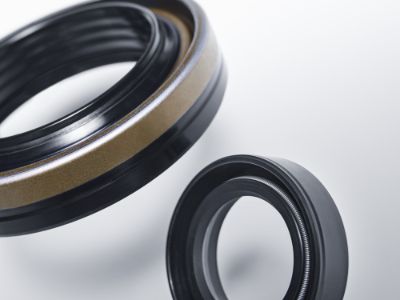
Radial shaft seals and axial shaft seals for applications with rotational motion
Let’s Talk about Your Project!
Request a Free Consultation and Find a Perfect Solution Customized for you.
Based on our assortment we create and develop an individual solution for your application – or we even develop from scratch a high-performance part for your product to ensure quality & safety. For expert advice and customized solutions tailored to your specific needs,
Let's talk!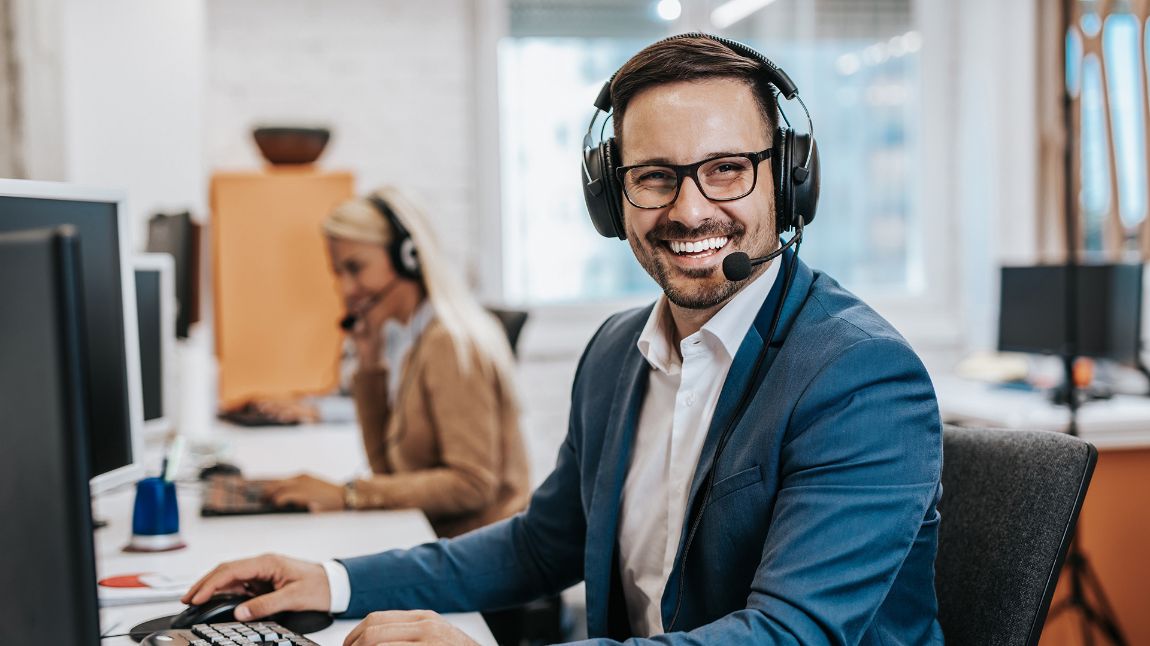
Related Downloads
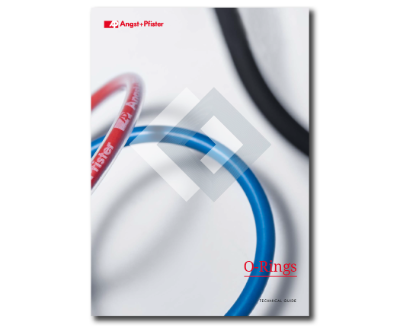
We make it work!
Just contact us and We will get back to you as quickly as possible!
Stay up-to-date!
Sign up for our newsletter today and receive our newest updates on products and latest industry trends!