
February 9, 2021
Meeting rising material demands
High-performance elastomers
Performance requirements for materials are high and becoming higher across all industries: Materials have to withstand conditions more extreme than ever before, such as high or low temperatures, aggressive liquids, gases or extreme physical stresses – and this with the expectation of the same or even longer service life. It is often a matter of guaranteeing the operational safety of machines and systems. In addition, the materials have to meet increasingly stringent legal requirements. These materials are rightly referred to as high-performance compounds.
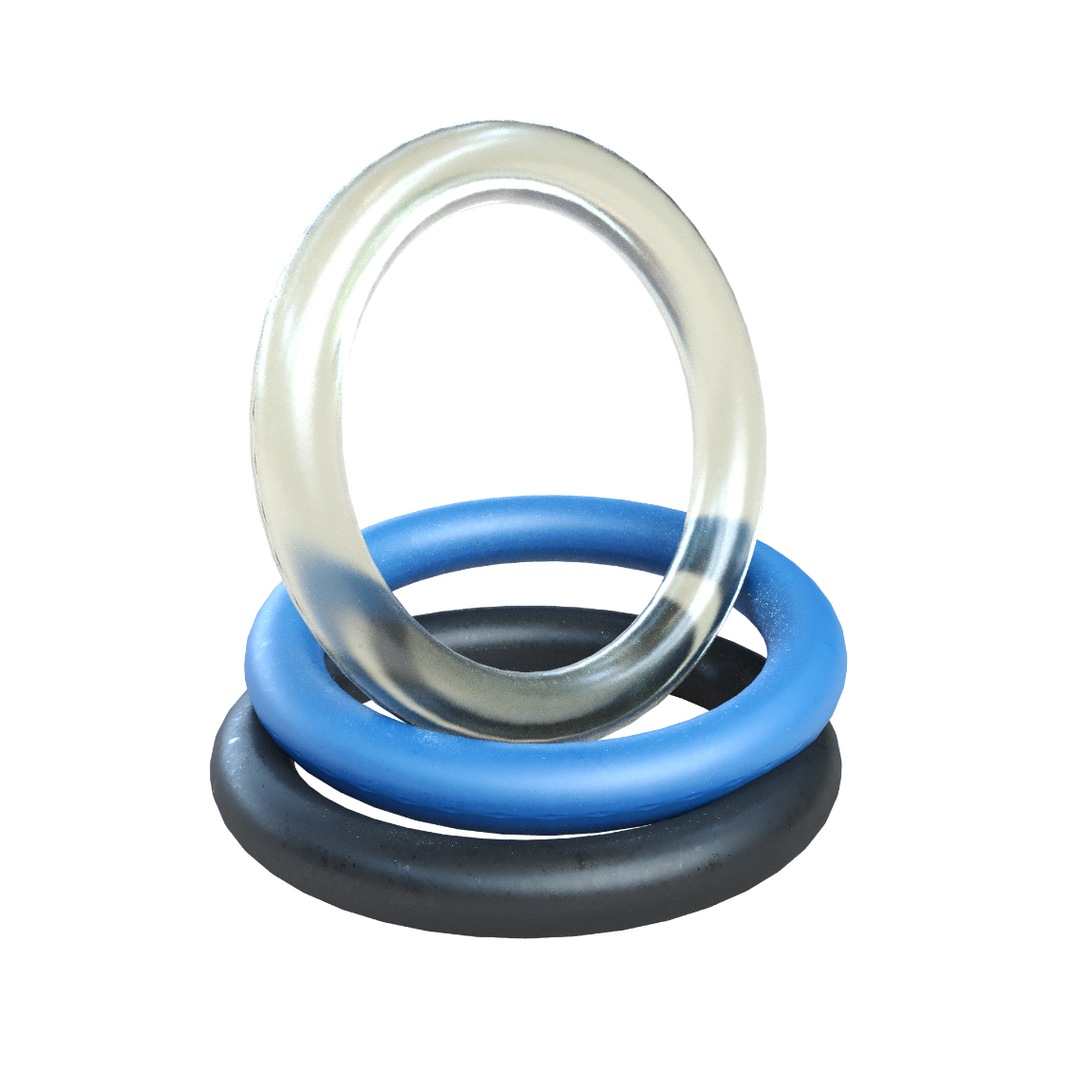
As these challenges become more demanding, anyone who wants to win through in international competition has to be able to count on their operational facilities running smoothly without a hitch. This requires machinery that lasts in order to avoid production downtime and operating losses. It goes without saying that a machine’s durability depends substantially on the quality of its components. Consequently, component materials will always require further development to adapt to new conditions and continually improve them. In this regard, compounding has become one of the key fields in engineering when it comes to high-performance elastomers. It is essential for application producers to know they have a specialist technology partner that they can rely on – with excellent blending and development capabilities.
Recognizing the importance
For many years now, Angst+Pfister has recognised the major importance of compounding for its customers, particularly its significance for the future and can lay to claim to significant experience in this area. Acquiring these skills was just the beginning – over the years, they have been constantly upgraded, extended and improved: Customers should be able to expect custom solutions at all times for increasingly challenging conditions – and in line with the most recent technological developments. For Angst+Pfister this means continuous learning, research, investing, and testing.
Elastomer compounding for sealing and antivibration technology is as much an art as a science. The expert combination of polymers and additives, and correct kneading time ensures that the resulting vulcanised elastomer bond has the desired physical properties and performance. And it means that the raw materials have good flow properties for processing and waste is minimised. Angst+Pfister knows that the bedrock of effective and efficient solutions is materials engineering and chemistry knowledge combined with development expertise and experience – as demonstrated by a comprehensive collection of formulae.
The next generation
Angst+Pfister’s PERTEC® is a newly developed generation of high-performance elastomers with excellent material qualities for a range of industrial uses. The ever expanding PERTEC® family includes various high-performance elastomers that have been granted all the international industry approvals. The back catalogue of projects, and satisfied customers, show that with PERTEC® Angst+Pfister has created a new high-performance material able to meet custom requirements for sealing technology solutions at the highest technological level. And that is not the end of it. Angst+Pfister analysed the markets and identified segments where new, high-performance compounds would bring significant improvement in industrial applications and offer customers a decisive competitive advantage.
PERTEC® NP FKM
In contrast to the conventional coating of materials, a new class of peroxide-cured PERTEC® NP FKM compounds has now been developed to improve performance based on nano-PTFE, prepared using the microemulsion technique – with extraordinary properties. It has very high abrasion resistance, is highly resistant to chemicals, and has a very low permeability. In spite of its high degree of hardness, it has very good tensile strength and contains no metal ions. This compound is available in a Shore A hardness of 70 – or in a harder version with a Shore A hardness of 80 for applications where high pressure is involved.
The advantages compared to the conventional method with PTFE powder are: avoidance of material accumulation, homogenous dispersion, an up to 40 % higher degree of filling (cf. 6 % for PTFE powder) for simultaneously good mechanical properties.
Angst+Pfister products typically made from PERTEC® NP FKM, are O-rings, moulded parts, and membranes, which are particularly suited for valves, pumps, and couplings for the pharmaceutical, food, and chemical industries.
PERTEC® CIP/SIP FKM
PERTEC® CIP/SIP FKM is a new, specialised, high-performance elastomer developed for use in CIP (Cleaning In Place) and SIP (Sterilisation In Place) systems. It is used in situations where a very high level of hygiene is mandatory, such as in the food processing, pharmaceutical, medical, and chemical industries. Application components and materials in these systems are exposed to aggressive chemicals (e.g. nitric acid or hypochlorite) in cleaning materials, as well as high concentrations of grease and extreme temperatures.
PERTEC® CIP/SIP FKM complies with all essential regulations of these industries. The very high fluorine content of PERTEC® CIP/ SIP FKM confers very good chemical resistance and resistance to very high temperatures up to +200 degrees Celsius. It shows very good abrasion resistance and very low permeability. This compound is available in a Shore A hardness of 75 – or in a harder version with a Shore A hardness of 85 for application where high pressure is involved.
Angst+Pfister primarily produces O-rings, moulded parts, membranes and dynamic seals from PERTEC® CIP/SIP FKM for use in the pharmaceutical, food, medical, and chemical industries.
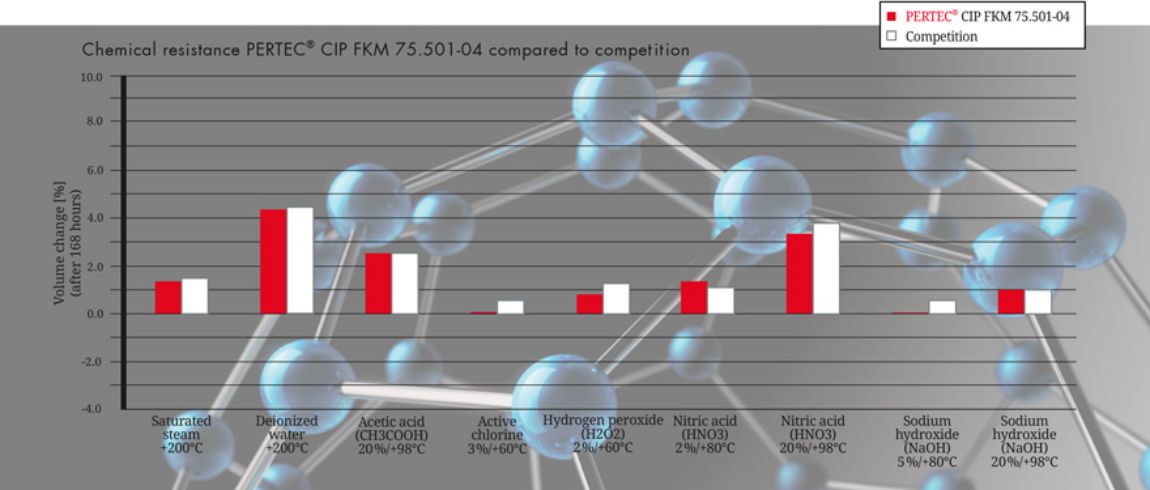
PERTEC® UP VMQ
PERTEC® UP VMQ is a new high-performance elastomer specially developed for uses in which absolute material cleanliness is mandatory. The name itself says this - UP stands for ultra-pure. The focus lies on uses for the food, pharmaceutical, and medical industries, where complete material sterility is the most important requirement. In these sectors there can be no contamination of the environment by the materials in use. The specific requirements are prescribed in various international regulations. PERTEC® UP VMQ complies with all global food contact regulations. Furthermore, all substances used in the compound are listed in the EU as well as the US food industry regulations.
PERTEC® UP VMQ is also characterised by very good mechanical qualities in a temperature spectrum from -60°C to +200°C. It has very good resistance to a multitude of aggressive chemicals, has very good tensile strength, and low VOC (Volatile Organic Compounds) content.
Typical Angst+Pfister products made of PERTEC® UP VMQ are O-rings, moulded parts, and membranes for drinking water applications and for uses in the pharmaceutical, medical, and chemical industries.
PERTEC® ST FKM
PERTEC® ST FKM is a high-performance elastomer developed by Angst+Pfister that is particularly suited for use in contact with steam and hot water, not least because of its high resistance at temperatures from +15 to +200 degrees Celsius. It is resistant to a multitude of aggressive chemicals, mineral oils, and grease as well as ozone, weather, aging, and is oxygen compatible with very low permeability. This compound is available in a Shore A hardness of 75.
The special mix means processing using the compression or injection methods is very economical and permits flexible and optimal custom production. The result is high quality and competitive prices.
The high concentration of fluorine ensures maximum resistance in exceptionally high temperatures. As a consequence, the material is particularly suitable for steam applications such as steam heating systems, steam injectors, gas atomizers (gas flares) and steam cleaners.
The main applications of PERTEC® ST FKM are O-rings, moulded parts and membranes for couplings, turbines, pumps, and valves, and for uses in the chemical industry.
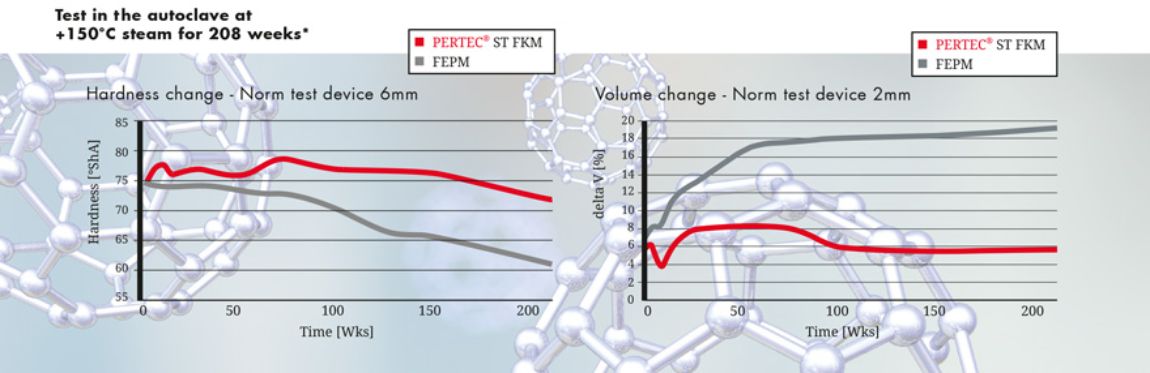
PERTEC® UP FKM
PERTEC® UP FKM is an advanced compound from this line of products. Similarly to the silicone elastomer PERTEC® UP VMQ, the purity of the material is crucial – and as such UP also stands for Ultra Pure in the compound description. This compound was developed specifically for the pharmaceutical, food processing and beverages industries. It meets all the major drinking water and food processing requirements of the relevant international regulations.
The formulation complies with the PAKs Category 1 requirements, aimed at potentially carcinogenic polycyclic aromatic hydrocarbons that must not migrate into food or beverages. The compound is known for its very good mechanical qualities in a temperature spectrum from –20 to +200 degrees Celsius. In addition, PERTEC® UP FKM is extremely resistant to aggress chemicals and absolutely suitable for use in steam and hot water. This compound is available in a Shore A hardness of 70.
PERTEC® UP FKM is primarily produced for O-rings, moulded parts for valves, couplings, pumps for the pharmaceutical, food processing and beverages industries.
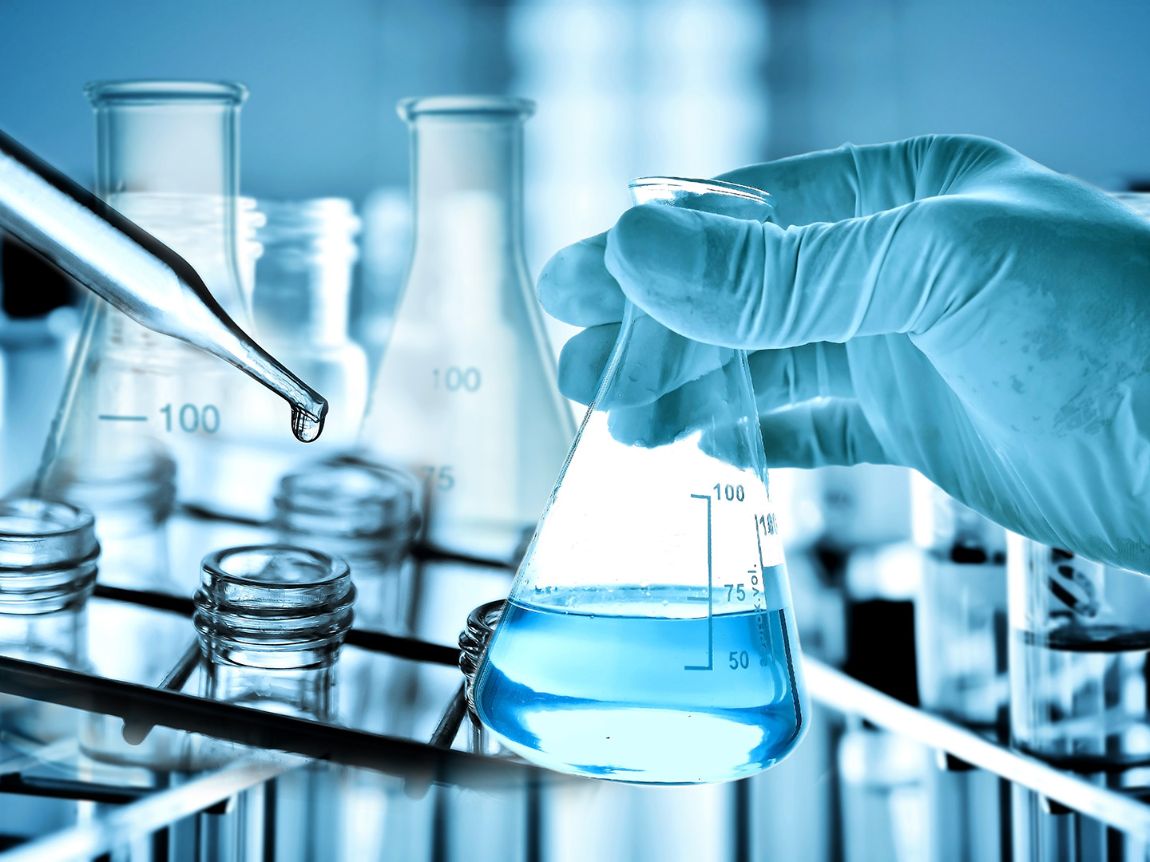
Get connected!
Let’s talk about your challenges and how Angst+Pfister can support you.
Your one-stop shop for industrial components
Dive into the extensive range of standard applications in the online shop of APSOparts with great benefits for efficient order processes!