Aby zaprojektować i opracować najlepsze rozwiązanie dla naszych klientów, Angst+Pfister wykorzystuje najnowsze narzędzia oprogramowania CAD do symulacji czasu życia i optymalizacji wydajności. Takie podejście zapewnia, że każdy produkt jest skrupulatnie zaprojektowany w najdrobniejszych szczegółach przed rozpoczęciem produkcji.
Integrując analizę metodą elementów skończonych (MES), symulujemy wydajność i optymalizujemy projekty pod kątem trwałości i wydajności. Takie podejście umożliwia precyzyjny dobór materiałów i walidację projektu, znacznie zmniejszając ryzyko awarii w krytycznych zastosowaniach oraz zapewniając najwyższą jakość i niezawodność.
Kluczowe kompetencje w skrócie
- Weryfikacja projektu: Płynna integracja CAD, MES i analizy przepływu formy zapewnia optymalizację projektów pod kątem trwałości, wydajności i możliwości produkcyjnych przed rozpoczęciem produkcji.
- Zwiększona niezawodność i trwałość: Precyzyjny dobór materiałów i symulacja wydajności znacznie zmniejszają ryzyko awarii w krytycznych zastosowaniach, dostarczając rozwiązania o najwyższej niezawodności i wydłużonej żywotności.
- Przyspieszony proces rozwoju: Zaawansowane technologie symulacji minimalizują cykle prototypowania i testowania, umożliwiając szybsze wprowadzanie produktów na rynek bez uszczerbku dla jakości i precyzji.
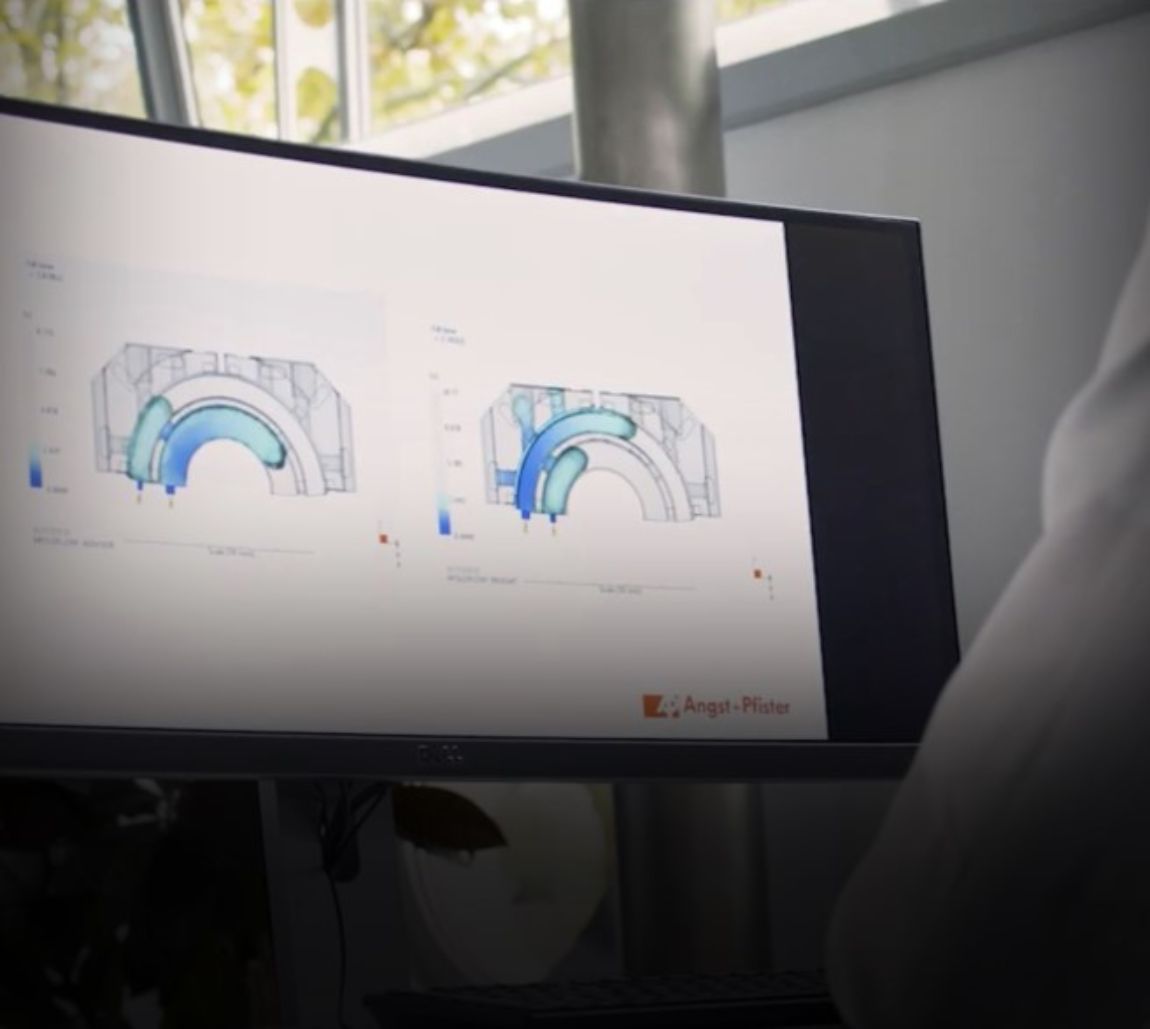
Precyzja na każdym kroku - proces projektowania i rozwoju rozwiązań
Krok 1 - Tworzenie rysunków 2D i złożeń 3D
Zaczynamy od projektowania wspomaganego komputerowo (CAD), wykorzystując zaawansowane oprogramowanie do tworzenia bardzo dokładnych rysunków 2D i złożeń 3D. Ten podstawowy krok umożliwia nam dopracowanie każdego szczegółu projektu, przygotowując grunt pod kolejne analizy, które optymalizują funkcjonalność i możliwości produkcyjne.
Krok 2 - Zastosowanie analizy elementów skończonych
Następnie wykorzystujemy analizę elementów skończonych (MES) do symulacji krytycznych zachowań fizycznych w fazie projektowania. Analizując reakcje na naprężenia/odkształcenia, rozszerzalność cieplną i skurcz, uzyskujemy cenne informacje, które minimalizują potrzebę szeroko zakrojonego prototypowania i testowania. Pozwala nam to opracowywać lepiej zoptymalizowane komponenty w krótszym czasie.
Krok 3 - Zapewnienie optymalnego przepływu materiałów i funkcjonalności
Aby udoskonalić proces produkcji komponentów gumowych, przeprowadzamy symulacje cyklu formowania wtryskowego za pomocą oprogramowania do symulacji wirtualnego formowania. Szczegółowe mapy kolorów ujawniają istotne dane dotyczące temperatury, przepływu ciepła, wzorów napełniania i ciśnienia wtrysku w formie. Te spostrzeżenia pomagają nam zapewnić optymalny przepływ materiału, funkcjonalność i jednolitą jakość we wszystkich gniazdach.
Porozmawiajmy o Twoim projekcie!
Poproś o bezpłatną konsultację i znajdź idealne rozwiązanie dostosowane do Twoich potrzeb.
W oparciu o nasz asortyment tworzymy i opracowujemy indywidualne rozwiązanie dla danego zastosowania - lub nawet opracowujemy od podstaw wysokowydajną część dla danego produktu, aby zapewnić jakość i bezpieczeństwo. Aby uzyskać fachową poradę i niestandardowe rozwiązania dostosowane do konkretnych potrzeb,
Porozmawiajmy!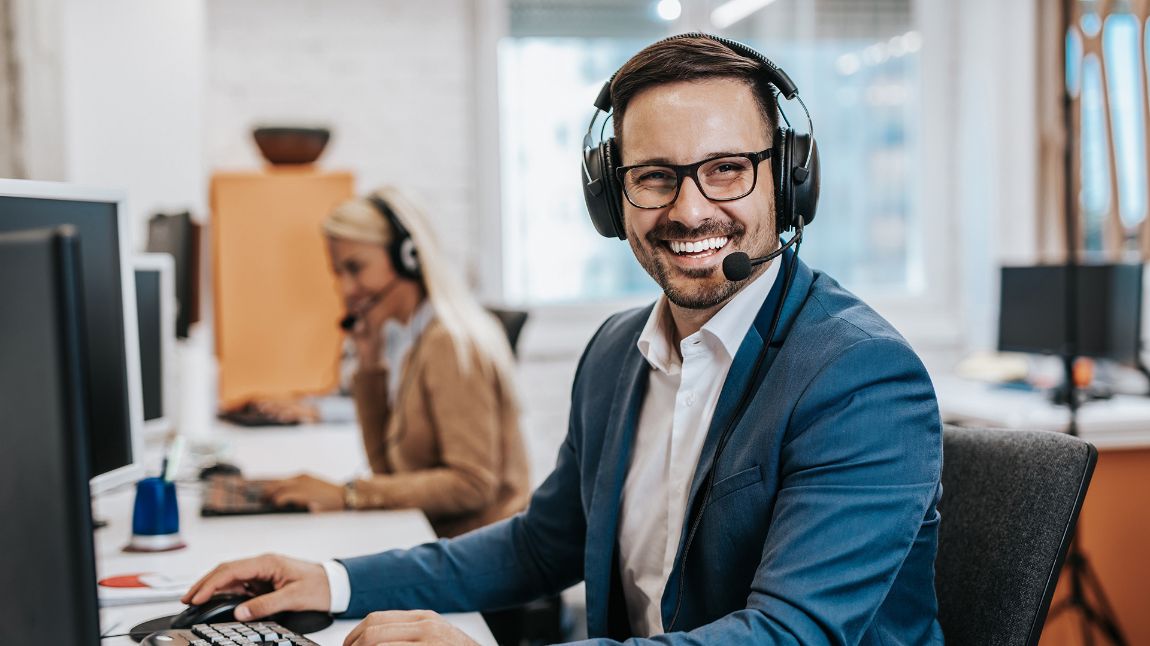
Zwiększ swoją wydajność dzięki naszym rozwiązaniom
Sprawiamy, że to działa!
Po prostu skontaktuj się z nami, a my szybko Tobie odpowiemy!
Bądź na bieżąco!
Zapisz się do naszego newslettera już dziś i otrzymuj najnowsze informacje o produktach i trendach w branży!