At Angst+Pfister, material and compound selection is more than a step in the engineering process - it’s the foundation of reliable, high-performance solutions. With over 2,500 unique material recipes for industries such as Food and Beverage, Pharma and MedTech, Oil & Gas, and Automotive, we deliver high-quality, customized formulations adapted to specific customer needs.
Leveraging decades of R&D expertise and state-of-the-art technology, we engineer advanced materials to meet the most demanding industry requirements. Our meticulous approach ensures innovation, reliability and precision in every compound we create, enabling our customers to excel in challenging applications.
Key Competences at One Glance
- Thorough R&D Expertise: Extensive knowledge in elastomeric and non-elastomeric materials for a wide range of industries and extreme conditions.
- Precision Testing and Analysis: Advanced in-house testing facilities ensuring materials meet and exceed performance expectations.
- Customized Solutions: Individually designed compounds optimized for specific applications, meeting industry regulations and customer specifications.

Precision at Every Step - the Art and Science of Material and Compound Selection
Step 1 - Understanding Challenges, Defining Solutions
The journey toward delivering cutting-edge materials starts with an in-depth understanding of the unique challenges faced by our customers. From extreme temperatures and exposure to aggressive chemicals to mechanical stress and regulatory compliance, our engineers assess every aspect of the application to define the precise material properties required.
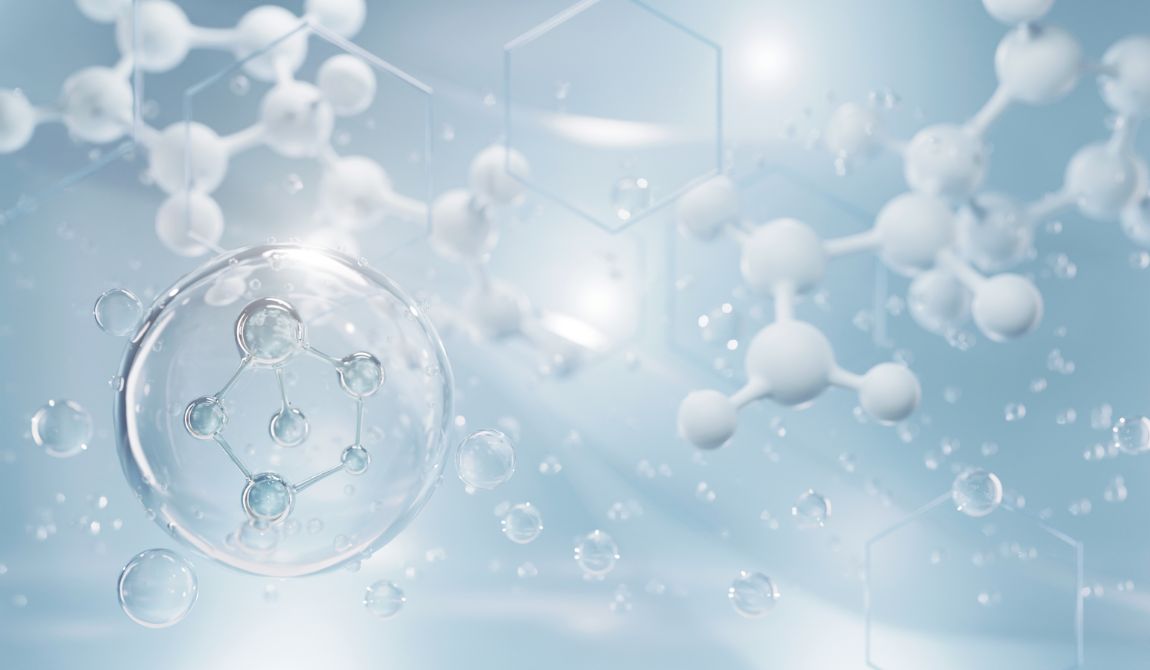
Step 2 - Thorough Research and Development
Our R&D team combines decades of expertise with advanced analytical tools to develop high-tech elastomeric and non-elastomeric compounds. Whether working with advanced elastomers like PERTEC® or high-performance plastics such as PTFE, we ensure each formulation is optimized for durability, reliability, and efficiency. This includes compliances checks for regulated industries and other challenges as well. As an example, we follow the current PFAS discussion carefully.
This development process includes:
- Evaluating raw materials through detailed chemical and physical inspections.
- Conducting comprehensive laboratory and application-specific testing.
- Leveraging advanced production technologies, such as automated ingredient dosing and high efficiency mixing machinery, for consistent quality and performance.
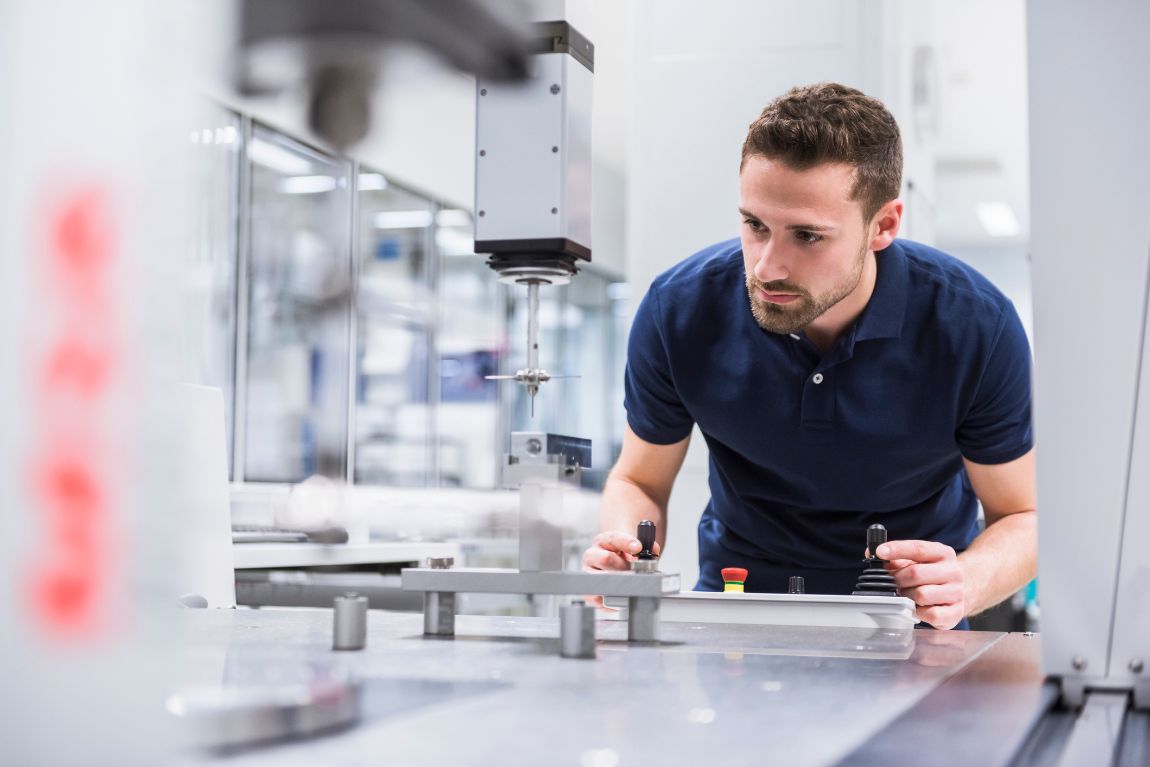.jpg)
Step 3 - Precision Testing for Optimal Results
Every high frequency compound undergoes extensive testing, far beyond typical industry compliance standards. Using sophisticated techniques—including thermogravimetric analysis, calorimetric testing, and surface morphology assessments - we evaluate critical performance factors such as chemical resistance, mechanical stress behaviour, and long-term durability.
Learn moreStep 4 - End-to-End Process Control
From material sourcing to final delivery, we maintain full control of the production process. This guarantees that every compound aligns perfectly with the required specifications and meets strict global regulatory standards.
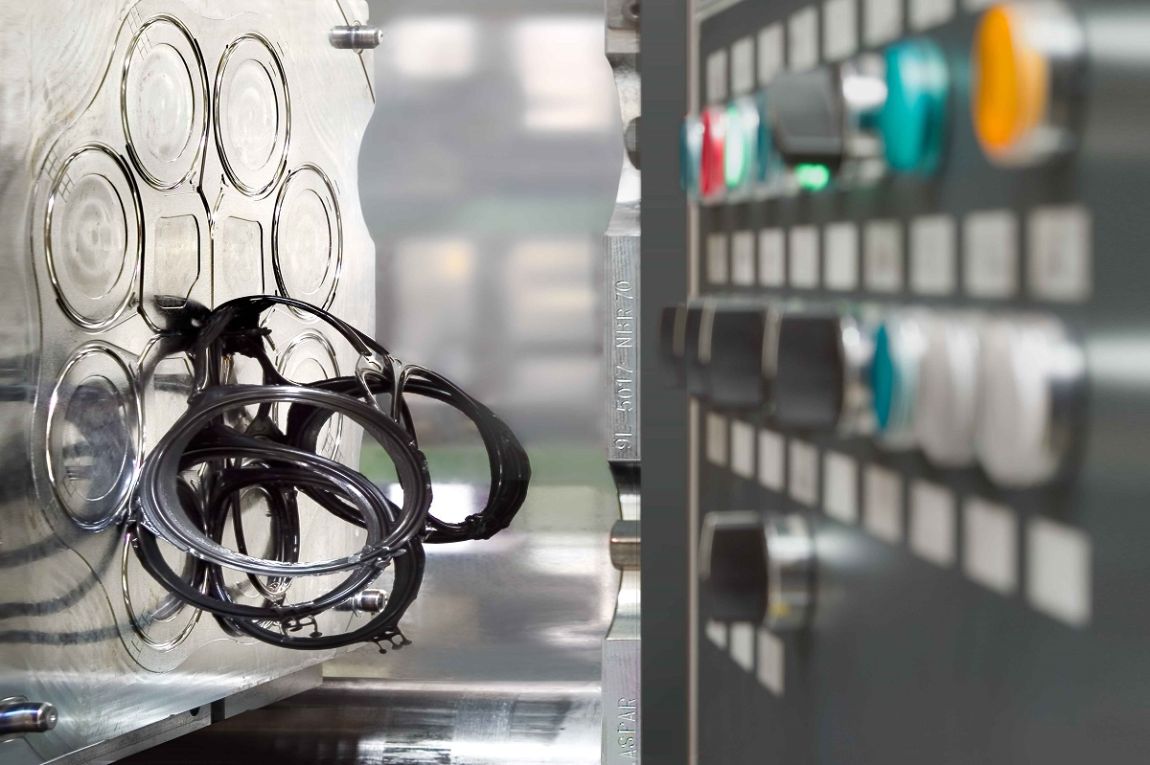
Turning Challenges into Triumphs: Customer Success
Fast Results Thanks to Experience, Design Skills and Material Knowledge
Warmhaus, a leading global producer of radiators and boilers, sought to develop silicone control buttons for its combi-boilers. These buttons needed to combine functionality, durability, and visual appeal for domestic installations while aligning with the company’s reputation for award-winning design innovation.
Challenge:
The buttons had to meet high standards for responsiveness, surface aesthetics, and thermal resistance, while coordinating with the boiler's design. Compounding the challenge, Warmhaus aimed for an ambitious market launch, requiring rapid prototyping and material approvals to ensure serial production began on time.
Solution:
Angst+Pfister’s engineers leveraged their extensive expertise in material science, design, and efficient development methods.
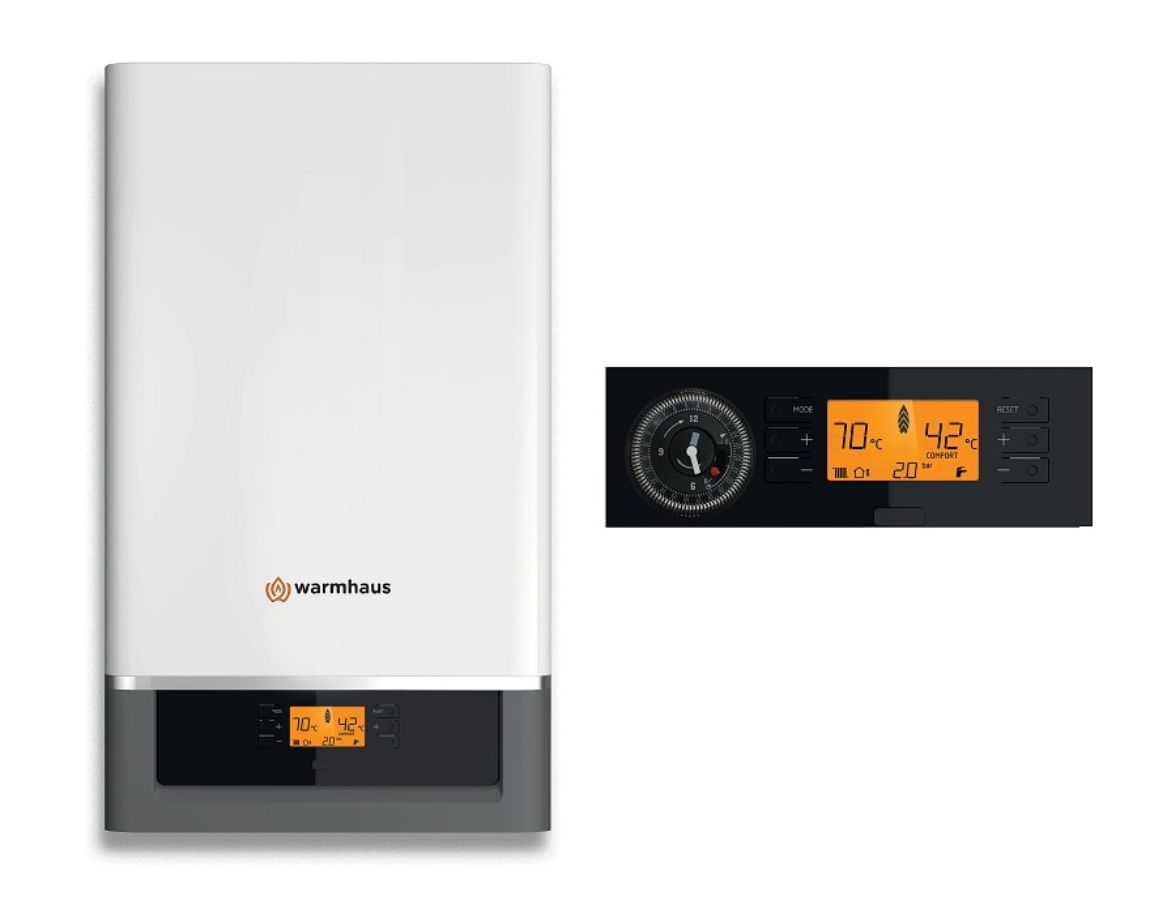.jpg)
The team created silicone-based control buttons tailored to Warmhaus’s specifications, including conductive elements and a “reset” function. The design integrated seamlessly with the boiler’s housing and color scheme. Rapid prototyping and material testing ensured production deadlines were met without compromising quality.
Result:
Warmhaus launched its boilers successfully, featuring high-performance, visually appealing control buttons that met stringent functionality and durability standards. Warmhaus praised Angst+Pfister as a valuable partner capable of delivering market-specific, high-quality rubber components under tight time constraints. This collaboration reinforced Angst+Pfister’s reputation for reliability, innovation and customer-focused solutions.
Let’s Talk about your Project!
Request a Free Consultation and find a Perfect Solution Customized for you.
Based on our assortment we create and develop an individual solution for your application – or we even develop from scratch a high-performance part for your product to ensure quality & safety. For expert advice and customized solutions tailored to your specific needs,
Let's talk!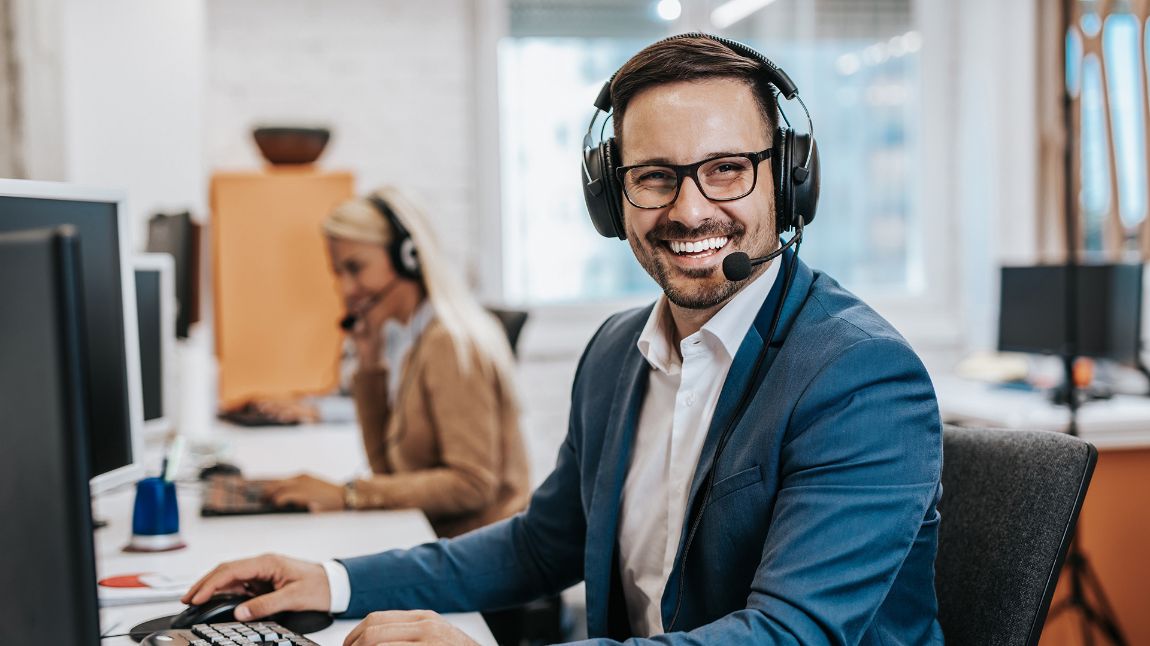
Related Topics
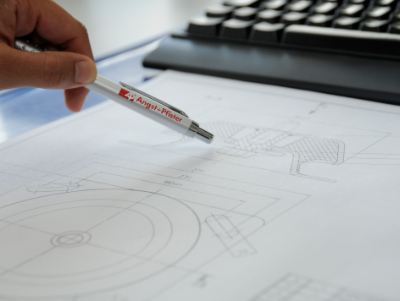.png)
We use CAD and Finite Element Analysis to design, validate, and optimize products efficiently..
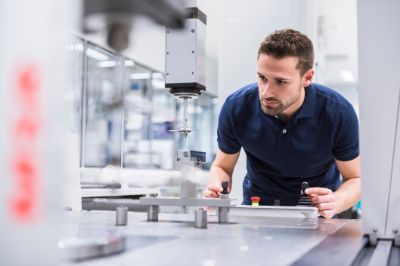.jpg)
We ensure product durability through advanced solution testing and validation.
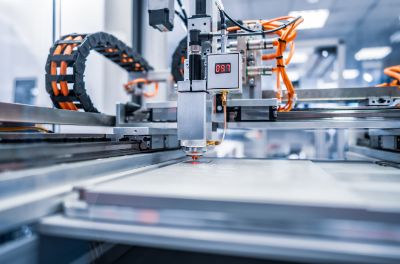
Our global production network utilizes advanced manufacturing technologies.
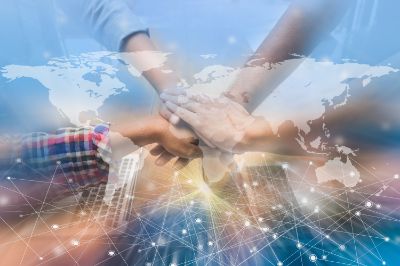
We provide local technical support in 24 countries.
We make it work!
Just contact us and We will get back to you as quickly as possible!
Request Your CAD Data Today
Ready to take the next step to optimize your product? Let our expert team assist you in achieving precision, efficiency, and performance.