To design and develop the best solution for our customers, Angst+Pfister utilizes the latest CAD software tools, for life-time simulation and performance optimization. This approach ensures every product is meticulously designed down to the last detail before going into production.
By integrating the Finite Element Method (FEA) analysis, we simulate performance and optimize designs for durability and efficiency. This approach enables precise material selection and design validation, significantly reducing the risk of failure in critical applications and ensuring the highest quality and reliability.
Key Competences at One Glance
- Design Validation: A seamless integration of CAD, FEA, and Mold Flow Analysis ensures that the designs are optimized for durability, efficiency and manufacturability before production begins.
- Enhanced Reliability and Longevity: Precise material selection and performance simulation significantly reduce the risk of failure in critical applications, delivering solutions with superior reliability and extended service life.
- Accelerated Development Process: Advanced simulation technologies minimize prototyping and testing cycles, enabling faster time-to-market without compromising on quality or precision.
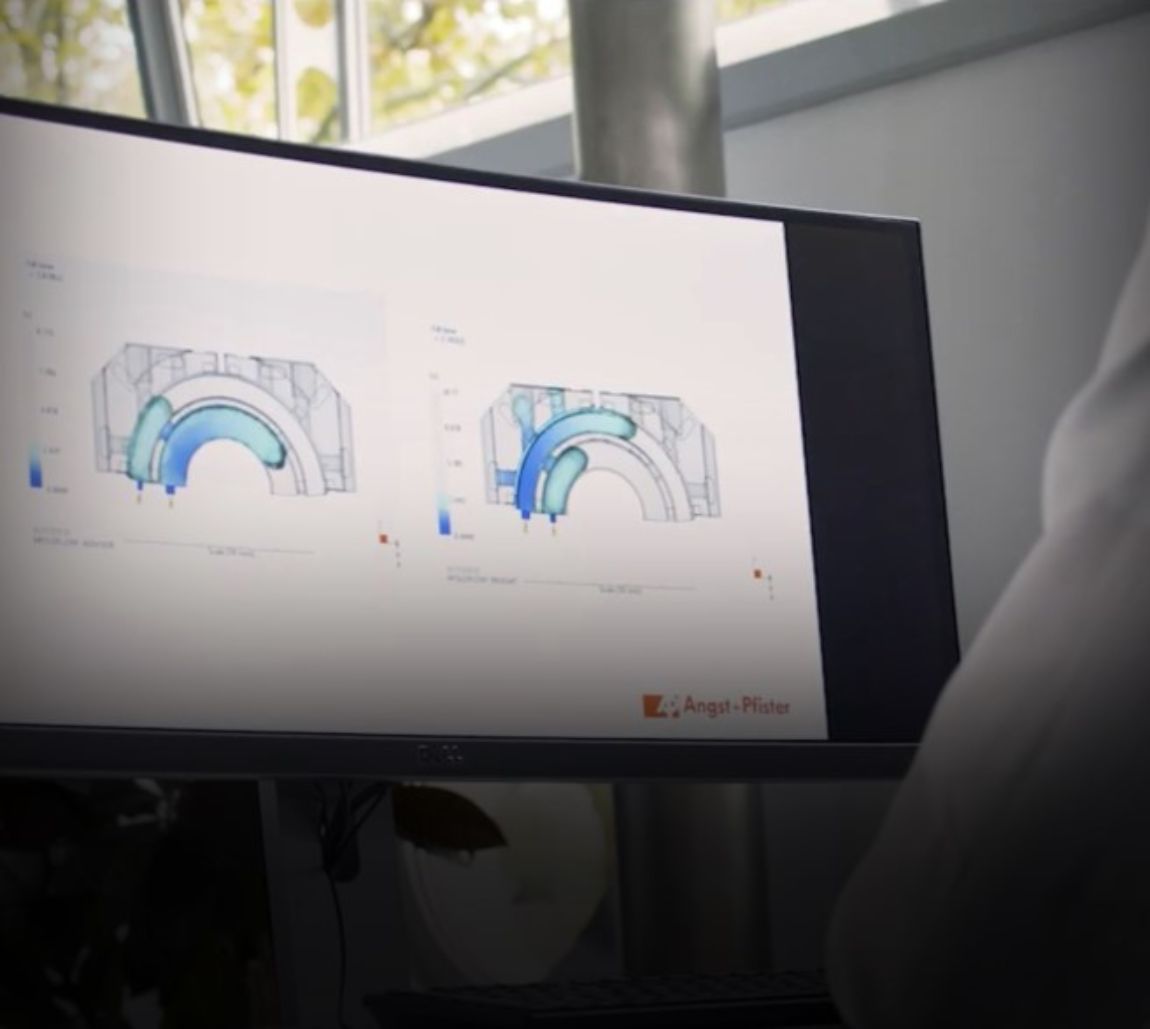
Precision at Every Step - the Process of Solution Design and Development
Step 1 - Creating 2D Drawings and 3D Assemblies
We start with computer-aided design (CAD), leveraging advanced software to create highly accurate 2D drawings and 3D assemblies. This foundational step enables us to refine every detail of the design, setting the stage for subsequent analyses that optimize functionality and manufacturability.
Step 2 - Employing Finite Element Analysis
Next, we employ Finite Element Analysis (FEA) to simulate critical physical behaviour during the design phase. By analyzing stress/strain responses, thermal expansion, and shrinkage, we gain valuable insights that minimize the need for extensive prototyping and testing. This allows us to develop better-optimized components in less time.
Step 3 - Ensuring Optimal Material Flow and Functionality
To perfect the manufacturing process for rubber components, we conduct simulations of the injection molding cycle by using a virtual molding simulation software. Detailed color maps reveal essential data on temperature, heat flow, filling patterns, and injection pressure within the mold. These insights help us ensure optimal material flow, functionality, and uniform quality across all cavities.
Let’s Talk about your Project!
Request a Free Consultation and find a Perfect Solution Customized for you.
Based on our assortment we create and develop an individual solution for your application – or we even develop from scratch a high-performance part for your product to ensure quality & safety. For expert advice and customized solutions tailored to your specific needs,
Let's talk!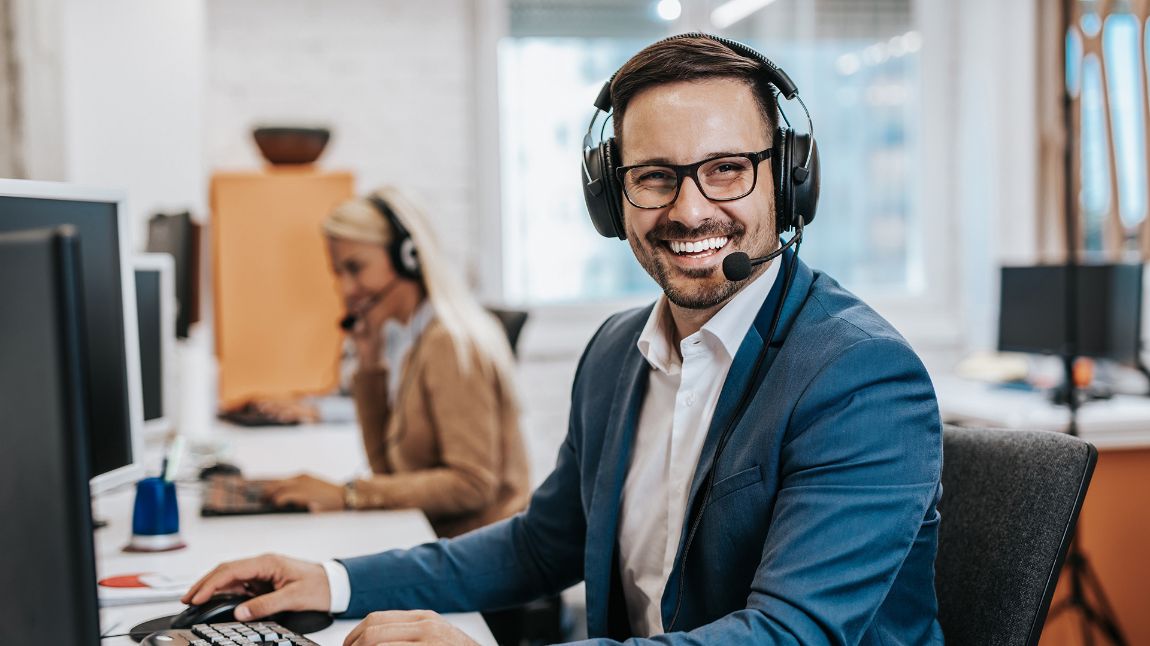
Related Topics
We make it work!
Just contact us and We will get back to you as quickly as possible!
Request Your CAD Data Today
Ready to take the next step to optimize your product? Let our expert team assist you in achieving precision, efficiency, and performance.