Using advanced technologies, we simulate real-world conditions to ensure every product meets the highest standards of durability and performance. Our capabilities include multi-axis dynamic testing, high-frequency evaluations for electric vehicles, and environmental tests like low-temperature (TR10) and ozone resistance.
Complementing these are advanced surface treatments such as sandblasting and zinc coating, enhancing bonding and corrosion resistance. With force-deflection, bonding strength, and creep testing, we guarantee reliability over time. Angst+Pfister’s commitment to excellence ensures solutions that meet the toughest challenges with unmatched precision and reliability.
Key Competences at One Glance
- Thorough Durability Assurance: Advanced technologies like multi-axis dynamic testing and environmental simulations ensure that products meet high durability and perform well under real-world conditions.
- Precise and Consistent Quality Control: Extensive tests such as elongation, compression, and ozone resistance for sealing guarantee consistent performance.
. - Optimized Performance for Emerging Demands: High-frequency elastomer testing and advanced bonding strength testing ensure our components address current challenges and are future-ready, especially for industries like electric vehicles.
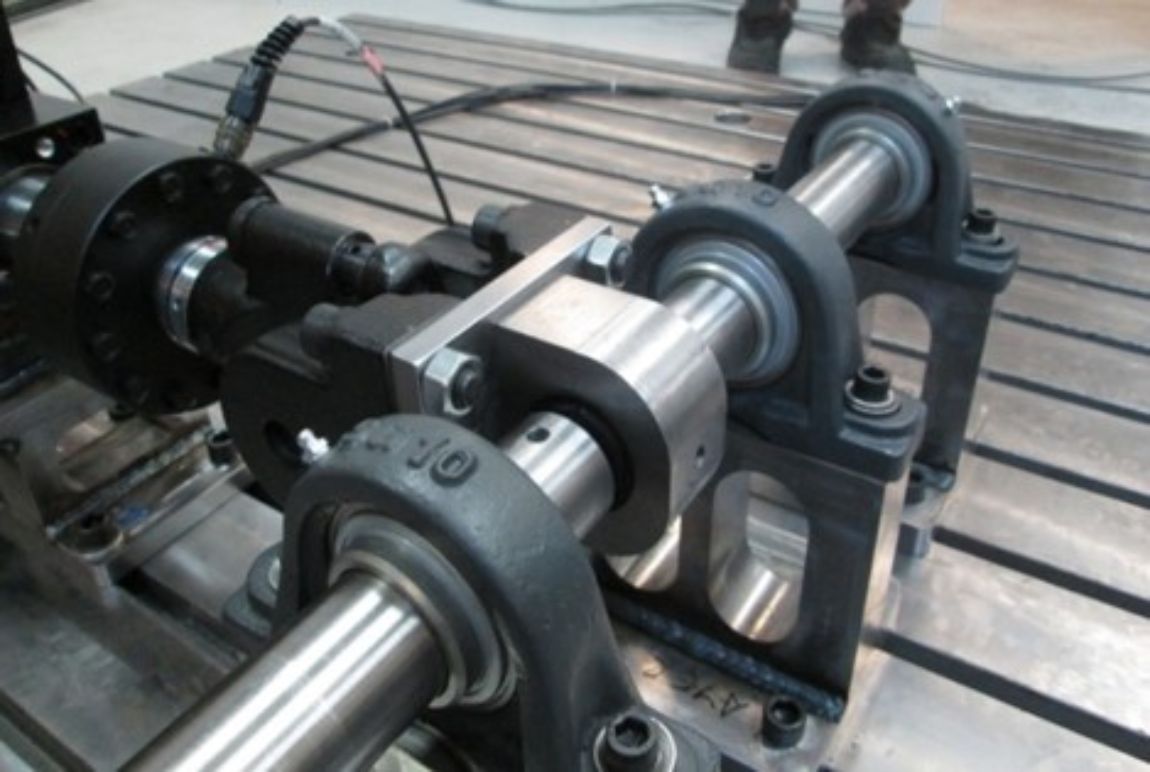
Precision at Every Step – The Process of Sealing Testing
Elongation Testing
Elongation at break, tensile strength or modulus can be precisely measured. This enables us to guarantee the performance of the seals itself and consistent quality overall. These testing machines are used in all our production facilities.
Compression Testing
Elastic recovery after being exposed to compression, a so-called compression set device is used. A sealing element can be placed within an autoclave and compressed for specifically defined periods of times, and in certain temperatures and contact media. The deformation is then measured, which can serve as a quality indicator.
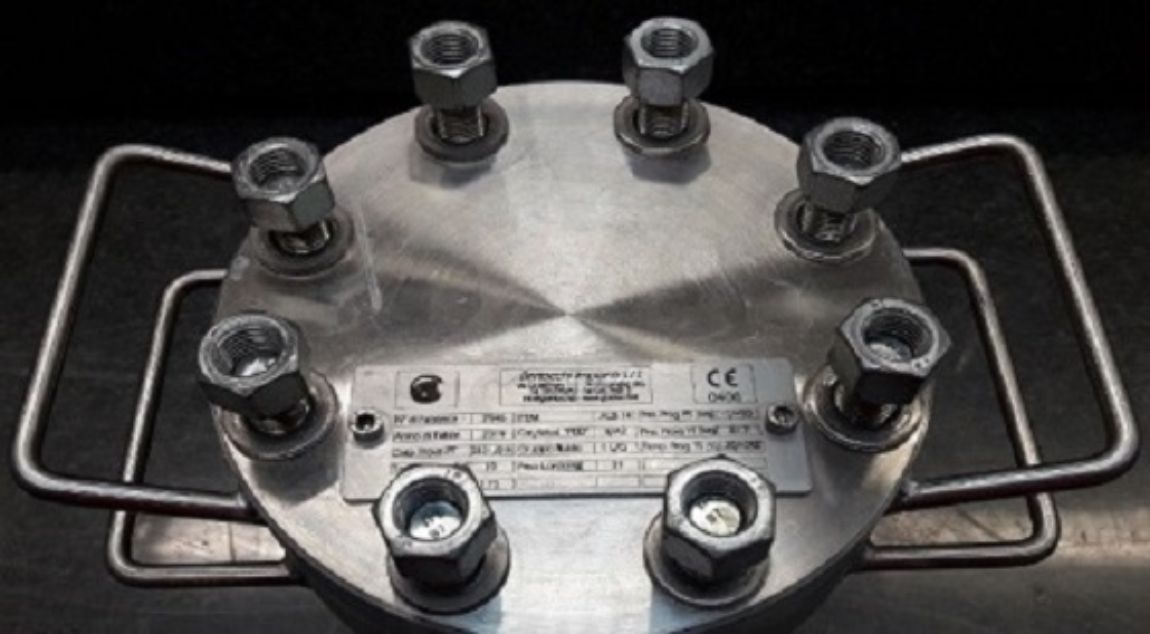
Additional Testing Methods for Elastomeric Solutions
Ozone Testing
Especially unsaturated polymers such as NBR, NR or SBR can develop cracks when deformed and used in normal ozone concentrations found in the daily environment. The resistance to ozone cracking can be considerably increased by the addition of special ozone-protection additives. During the ozone test, a sample is exposed to a specific ozone concentration while being stretched for a given percentage and time period. Once the test duration reaches the defined time period, the specimen is visually inspected for cracks. If no cracks are detected, the sample passes the test.
Low-Temperature Testing (TR10):
The TR10-value is the temperature at which a specimen that was stretched by 25% or 50% at room temperature, then recovers by 10% after gradually de-freezing it from a temperature below its glass transition point. Furthermore, this test shows the progressive defrosting behavior and the temperature dependent elasticity of the rubber material. For this reason, the TR-10 test is one of the most informative cold tests for O-rings and many other sealing applications.
Precision at Every Step – The Process of Antivibration Solution Testing
Force-Deflection Single-Axis Testing
Elastomer products can be defined by their reaction force against a deformation and force-displacement values are the basic identification for these properties. Angst+Pfister has the necessary infrastructure to characterize antivibration products with a wide range of force and frequency bands – starting from 10kN up to 250kN static characterization and from 1Hz up to 250Hz dynamic characterization.
Multi-Axis Dynamic Testing
Before releasing a finished, newly developed and value-adding product, durability needs to be ensured. Angst+Pfister uses linear and angular actuators, which can be combined to conduct multi-axis durability tests or can be used individually for different purposes. The linear actuators have a maximum 50kN force, while the angular actuators offer a 545Nm torque with ±45° rotation capability. Since the accuracy between field tests and laboratory tests is quite important, our actuators are also capable to run a Road Load Data (RLD) to more precisely verify the laboratory results. This test can be carried out under temperature conditions anywhere between RT and +200°C.
Surface Treatment and Coating Quality
At Angst+Pfister, we utilize advanced testing methods to ensure the quality and durability of surface treatments and coatings for our components. These methods verify cleanliness, bonding performance, and resistance to environmental factors.
Surface Cleanliness Testing
- Sand Blasting: Assesses surface cleanliness and smoothness by applying sand particles under controlled conditions. The method is used to verify the removal of dirt, rust, and imperfections while ensuring a surface suitable for optimal bonding.
- Degreasing Validation: Our degreasing line, with ten pools dedicated to cleaning and preparation, ensures surfaces are free of oil, dirt, and residues. Tests confirm that these conditions are met to support effective bonding.
Coating Performance Testing
- Phosphating Process Control: Includes 17 stages that ensure surfaces are free of contaminants, adequately treated for increased bonding area, and resistant to corrosion. Testing verifies uniformity and effectiveness of the phosphate layer, crucial for subsequent applications.
- Zinc Coating Durability Testing: Consists of 15 process steps designed to evaluate coating quality. Coating thickness is tested to meet the required 8–12 microns, with 10 microns achieving up to 250 hours of salt spray resistance. White or yellow passivation options (Cr+3) are tested for specific performance characteristics.
Bonding Strength Testing
Bonding strength tests serve as a performance indicator for surface preparations and vulcanization processes. After the vulcanization has completed, the rubber-metal components then move to our quality lab for a destructive bonding test. For a proper process quality, a complete rubber to rubber tear should occur.
Electrical Conductivity Testing
Angst+Pfister owns automation machines to measure the conductivity of buttons which are used in combi-boiler machines. In the automation, electrical resistance limits are identified. If the values are outside the set limits, the machine is automatically cutting the parts. This process therefore prevents customers from receiving parts of insufficient quality.
Creep Testing
Creep is a characteristic common to elastomer elements. It is an increase in elastic deflection, caused by a load and the resulting strain in the elastomer. In practice, the increase in elastic deflection caused by creep in isolating elements is, in most cases, negligible. For specific applications we perform creep tests. Creep measurements carried out on test pieces are valid for years and, considering the linear pattern of creep curves, make it possible to extract measurements over time. The additional elastic deflection caused by creep is the same in the first 24 hours as it is in the following 20 years.
High Frequency Testing Methods for Antivibration Solutions
The importance of electrical vehicles (EV) has increased in last few years, which results in new challenges. Electrical engines are fundamentally different from conventional internal combustion engines in terms of vibration characterizations. Up until now, a dynamical characterization between 50-400Hz for antivibration components was sufficient, but EV systems nowadays shift this value to 3000Hz and the focus from vibration to noise.
Angst+Pfister’s new investment, a high frequency elastomer test bench, is a combination of a modal shaker and a high-tech dynamic test bench that allows us to develop and validate antivibration components in a wide range of frequencies (50-3000Hz).
Let’s Talk about your Project!
Request a Free Consultation and find a Perfect Solution Customized for you.
Based on our assortment we create and develop an individual solution for your application – or we even develop from scratch a high-performance part for your product to ensure quality & safety. For expert advice and customized solutions tailored to your specific needs,
Let's talk!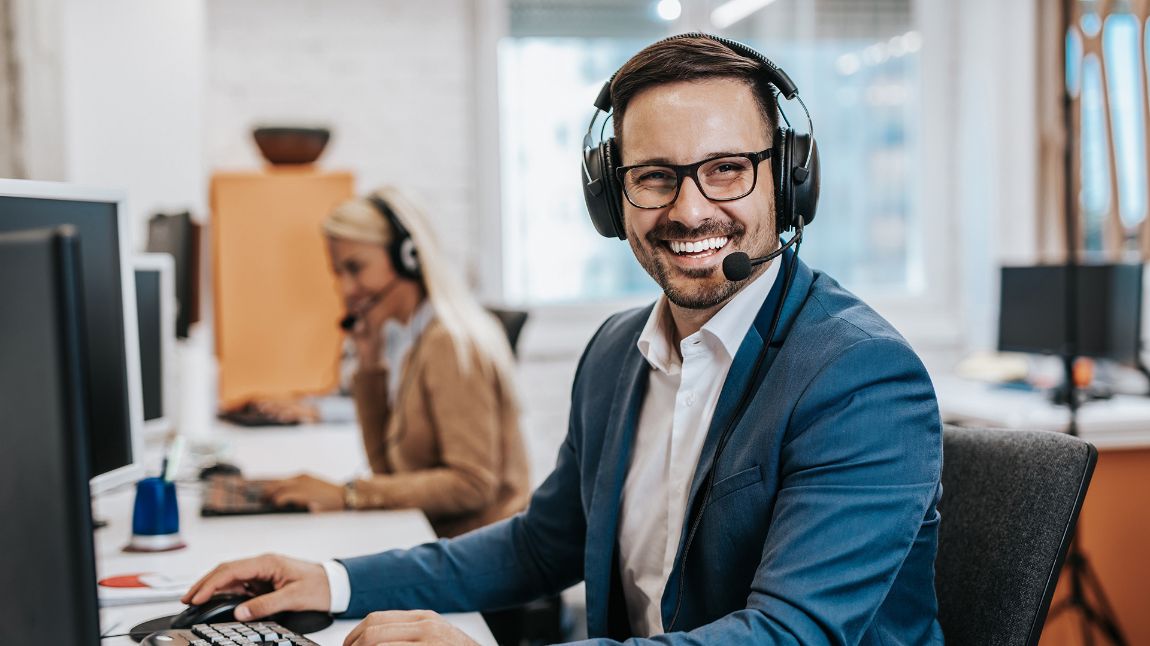
Related Topics
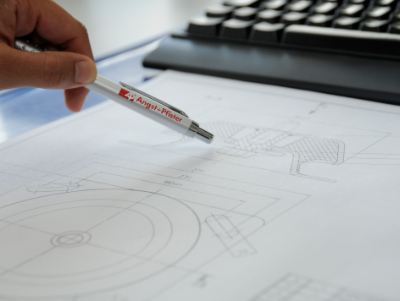.png)
We use CAD and Finite Element Analysis to design, validate, and optimize products efficiently..
With customized material formulations we ensure high performance solutions.
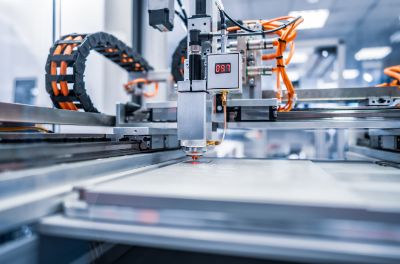
Our global production network utilizes advanced manufacturing technologies.
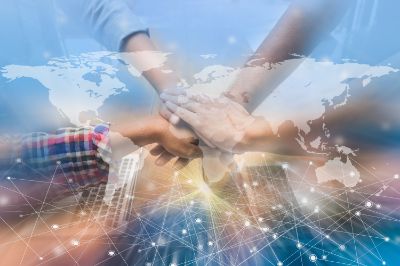
We provide local technical support in 24 countries.
We make it work!
Just contact us and We will get back to you as quickly as possible!
Request Your CAD Data Today
Ready to take the next step to optimize your product? Let our expert team assist you in achieving precision, efficiency, and performance.