Veröffentlicht von Angst+Pfister am 22. September. 2020
Auf der Agritechnica 2015, der weltweit größten Fachmesse für Landtechnik, stellte Krone eine innovative Maschine vor: den ersten Pelletierer, der auf dem Feld zum Zeitpunkt der Ernte in einem Arbeitsgang Pellets produziert, die direkt an Einzelhandelskunden geliefert werden können. Der „Premos 5000“ wird von einem Traktor gezogen und sammelt Stroh, das dann von zwei Matrizenwalzen zu Strohpellets gepresst wird. Die Pellets dienen sowohl als Tierfutter als auch zur Beheizung von Gebäuden.!
Technische Herausforderungen meistern
Krone suchte nach einer besseren Möglichkeit, das Getriebe abzudichten, da Schmutz zu schnell in die inneren Maschinenteile eindrang und die Antriebswellen überlastete. Die verwendeten Metallwellendichtringe entsprachen nicht den hohen Qualitätsstandards von Krone. Das Unternehmen konzentriert sich nicht nur auf innovative, sondern auch auf qualitativ hochwertige Produkte, die kontinuierlich verbessert werden – genau das, was seine Vor diesem Hintergrund wandten sich die Verantwortlichen von Krone an Jan-Ole Rienhoff, Product Application Engineer bei Angst+Pfister Deutschland, mit der Frage: „Würde es mit Gummi besser funktionieren?“
Angst+Pfister entwickelt und liefert alle Arten von Wellendichtungen in unterschiedlichsten Größen für eine Vielzahl von Anwendungen und greift dabei nicht nur auf sein umfangreiches Sortiment an Standardprodukten zurück, sondern entwickelt auch kundenspezifische Lösungen „Anfangs waren wir uns nicht hundertprozentig sicher, ob wir dieses Problem lösen können“, erinnert sich Jan-Ole Rienhoff. Aber er wollte die Herausforderung annehmen und besprach die potenziellen Probleme offen mit Krone. Die Schwierigkeit lag vor allem in der Größe der Wellendichtungen mit einem Wellendurchmesser von 900 Millimetern. Die Dichtungen müssen verhindern, dass Stroh und Schmutz in das Getriebe
Gemeinsam Lösungen finden
Die Frage war, welche Art von Design und Vorspannung die Dichtungsfestigkeit der beiden großen Ringe erhöhen würde. Darüber hinaus mussten sie robust genug sein, um etwa tausend Betriebsstunden zu überstehen – eine Maschine ist zwischen 200 und 500 Stunden pro Saison in Betrieb. „Dank unseres Know-hows sind wir auch in der Lage, technisch schwierige Projekte in Angriff zu nehmen“, sagt Jan-Ole Rienhoff. Die Idee bestand darin, einen Radialwellendichtring mit metallischer Verstärkung zu entwerfen, um seine Robustheit zu erhalten. Um den Innenbereich der Maschine optimal zu schützen, benötigte der Ring eine axiale Lippe mit zusätzlicher Fettschmierung, um die Leistung zu verbessern. Die Ingenieure von Angst+Pfister erstellten eine grobe Schätzung für die Konstruktion und Produktion der Wellendichtungen. Dann ging es darum, sich die Details anzusehen, die Werkzeuge herzustellen und die Prototypen zu fertigen.
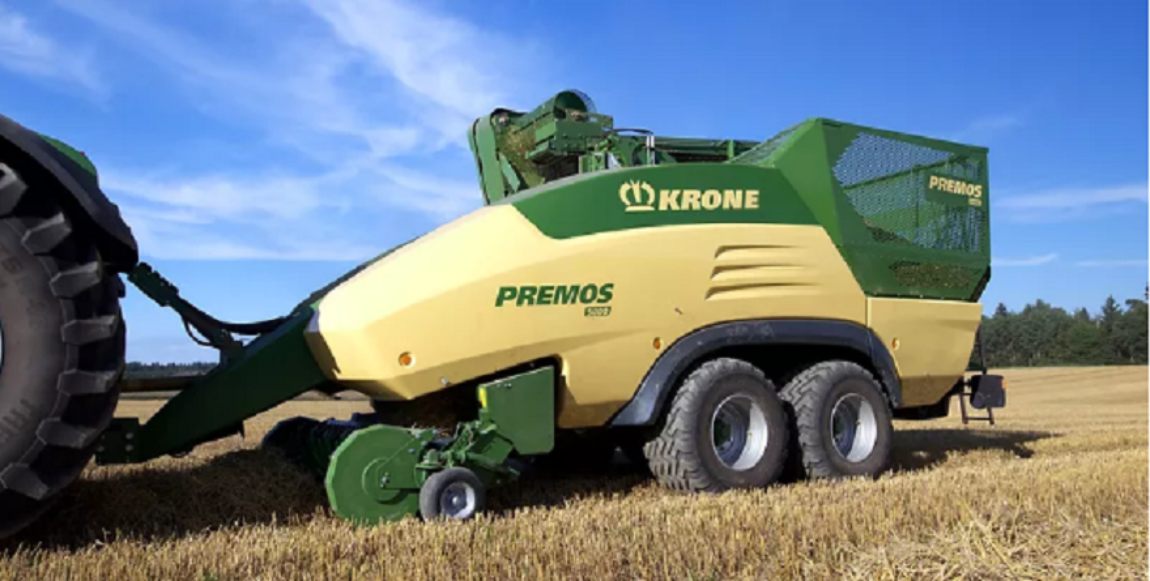
Proaktiv – vom Entwurf bis zur Installation
Angst+Pfister verfügt über eine hervorragende Produktionsplattform. „Wir standen also in ständigem Kontakt mit der Produktion“, erklärt Jan-Ole Rienhoff, der die Machbarkeitsstudie unterstützte, um herauszufinden, was, wenn überhaupt, hergestellt werden könnte. Eine weitere harte Nuss war die Vorspannung. „Wenn sie zu schwach ist, dichtet die Dichtung nicht richtig ab – wenn sie zu stark ist, schließt sie zu schnell“, erklärt Jan-Ole Rienhoff.
Der erste Prototyp fiel sofort aus, weil Strohhalme in das Getriebe eindrangen. Jan-Ole Rienhoff fand sich bald darauf in der Krone-Werkstatt wieder und analysierte zusammen mit dem Kunden das kontaminierte Getriebe. Die gemeinsame Analyse und wiederholte Toleranztests zeigten, dass Krone eine einfache Anpassung am Getriebe vornehmen konnte, um die Vorspannung an der Dichtlippe zu erhöhen. Die nächsten montierten Getriebe bestanden alle Tests bei Krone und sind bereits bei den ersten Landwirten im Einsatz. Angst+Pfister hat die Wellendichtungen inzwischen in die Produktion aufgenommen und liefert sie als Standardprodukt. Als zusätzlichen Service wurden auch detaillierte Montageanleitungen bereitgestellt.
Angst+Pfister hat die Ware zur Zufriedenheit des Kunden geliefert. „Mir war es wichtig, dass das Projekt mehr ist als das Abarbeiten eines Lastenheftes und dass wir auf Basis unseres Grundlagenwissens gemeinsam das Problem diskutieren, verschiedene Ideen und Optimierungen betrachten und gemeinsam eine Lösung erarbeiten“, erklärt Kai Lüpping, der bei Krone die Konstruktionsverantwortung für den Premos hat.
Wir sorgen dafür, dass es funktioniert!
Nehmen Sie einfach Kontakt mit uns auf und wir werden uns so schnell wie möglich bei Ihnen melden!
Entdecken Sie Ihren Weg zur Innovation
Lernen Sie unser Know-how in verschiedenen Bereichen kennen und arbeiten Sie mit uns zusammen, um maßgeschneiderte technische Lösungen zu finden.