Published by Angst+Pfister on February 2021
Work together, grow together – Angst+Pfister commits to winning over customers on the basis of performance for every single project, while delivering market advantages for the customer. This makes for great partnerships. And is also the reason the Belgian company LAG Trailers switched step-by-step to seals made by Angst+Pfister. As market leader for silo semi-trailers in the Benelux countries, LAG today requires seals that are food approved, made with the best production method to guarantee top quality – and with optimised production and logistics so that the price is also a winner.
Years of innovation and growth mean that LAG Trailers is today a leading manufacturer of road transport vehicles – including the tipping silo semi-trailer. The most popular one is the undisputed market leader in the Benelux countries. LAG is not only at home in the Benelux countries but also has sales and service centres in Scandinavia, Great Britain, Germany and eastern Europe. The company is headquartered in Belgian Bree and employs around 430 skilled and experienced workers.
Performance that impresses
Angst+Pfister has supplied LAG with fluid technology for some time now, more specifically the Storz couplings that simultaneously contain silicone or PTFE seals. “When talk turned to this type of seal, this was when our team became involved,” relates Jan Boomsma, Product Application Engineer, Sealing Technology. The package of couplings and seals offered the customer definite benefits. As a result of the positive experience of this project, LAG came back to Angst+Pfister when looking for a supplier for other seals. This time the seals were required for the hatches and filling ports of the silo semi-trailer – with relatively large diameters between 432 and 700 millimetres. The hatch and filling ports are closed with a cap, and the seal had to be attached to the silo semi-trailer itself.
As the silos also carry food stuffs, the seals have to have the corresponding approvals. LAG utilises NBR rubber (nitrile rubber) to deal with fatty or oily tank loads and requires approval from the Food and Drug Administration (FDA) of the United States of America. “Angst+Pfister offers a wide range of materials. In our range, we have a standard product of NBR rubber with approval for use in the food industry,” recounts Jan Boomsma. The homework for this section of the requirements had already been completed.
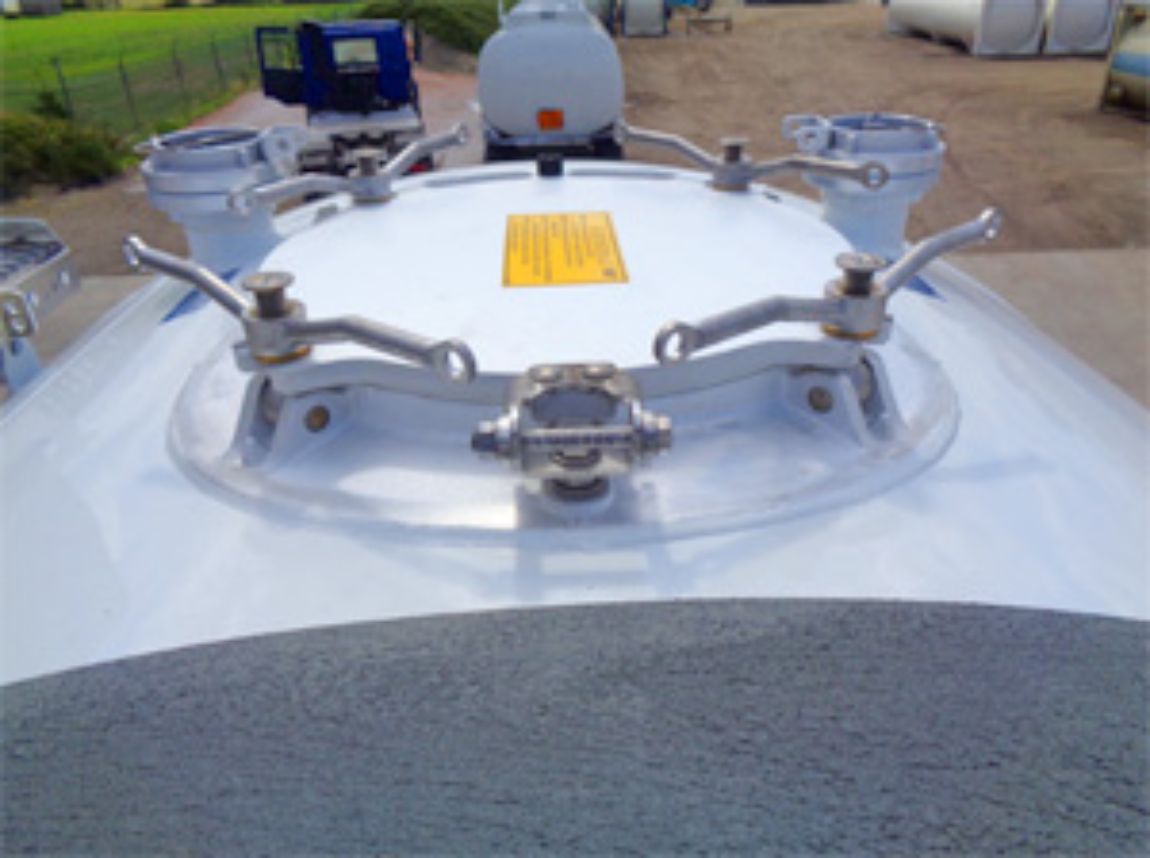
Consultation for production processes
“It is not easy to find seals like these of a reliably high quality,” says Rudi Langens, Senior Approvals of LAG Trailers N.V.. However, the engineers of Angst+Pfister were able to offer the desired seals in two versions, and explained to the customer the differences in price and quality. On the one hand there were cheaper extrusion parts designed as rings. “On the other hand, we suggested a pure injection moulding method whereby the parts are vulcanised to rings,” explains Jan Boomsma. In addition, Angst+Pfister suggested three different contractual periods which would guarantee the customer a set price for a set period of time. This allowed Angst+Pfister to optimise the production volume and processes, and make them economical – to the benefit of the customer in terms of price and logistics.
“In principle, it was a simple seal, but if there was not going to be a clean fit there might be problems with closing and opening the cap – or the seal might be dislodged from the groove. Injection moulding has a distinct quality advantage in this case – due to the smooth surface and the exact dimensions for serial production,” notes Jan Boomsma. Injection moulding parts seal better and are better at keeping within the tolerances. They are accurate to within 0.2 millimetres – in comparison to the 0.8 millimetres of extrusion parts. That makes assembly easier and the rings more durable. This is why LAG went for the more expensive injection moulding parts with a supply agreement across the entire supply chain for two years.
Growing together
“I visited the customer several times during the project and discussed numerous details with their engineers and buyers,” says Jan Boomsma. Open communication with the customer is absolutely crucial for projects like these – and for the engineers of Angst+Pfister the insights gained are always interesting. It is a matter of winning the trust of the customer.“ As the quality of these seals is exceptionally important for our silo semi-trailers, we approached this project with a great deal of care,” says Rudi Langens. Angst+Pfister responded in a very professional manner – right through from the sample tests to serial production.
LAG has been using the seals for over two years now. “The quality and availability is first class,” extols Rudi Langens. For this reason, LAG has switched step-by-step to Angst+Pfister for all similar components in order to ensure quality and quantity. “The professionalism and knowledge of the engineers convinced us to broaden our partnership.”
Get connected!
Let’s talk about your challenges and how Angst+Pfister can support you.
Discover Your Path to Innovation
Get to know our expertise in various fields and and partner with us for customized engineering solutions.